The responsibility of today’s emergency responder continues to expand into many facets of technical rescue. Within this area is an increase in incidents that are significantly more complex in nature. This can certainly be the case when there is a mixture of heavy vehicles that share our nation’s roads and highways with passenger vehicles. These extrication scenes can produce scenarios that will test both the capabilities of the responders and the equipment and skills in their “toolbox” (photo 1). Preparation and familiarization are two keys for overall success at these scenes.
This area of expertise requires a bit more capability than just bending and ripping metal; many times these incidents require a strong background in heavy lifting. Knowing the lifting capabilities of your equipment and having resources at your disposal that you can call upon to move heavy loads are vital to have. However, the crew cannot sit idly by while waiting for these resources to arrive; the crew must be capable of moving these objects with the equipment that is on the arriving apparatus. Many rescue companies boast of being able to handle these emergencies, but fall short in the logistics department. For example, if your department is responsible for handling an emergency of this nature, here is a list of a few critical pieces of equipment (besides the hydraulic extrication tools) that are vital to have:
Wire Rope Cables and Chokers – Wire should be inspected regularly and be free of any kinks, broken strands or fatigued bends in them. They should also have loops built into each end.
Chains and Shackles – Alloy lifting chain, grade 8 (80) or 10 (100) with marking tag in place should be carried (photo 2). Chains should not have any stretch points, twisted links or nicks in the links.
Nylon & Polyester Slings – Seamless slings with ID tags, along with corner protection pieces, will be instrumental on the extrication scene.
Rigging Rope and Rigging Hardware – Many companies “retire” older life safety rope and hardware and assign the usage for heavy rigging. Be sure not to inter-mix these with true-life safety usage equipment.
The Commercial Vehicle Industry
No matter what the product, odds are very good that it got to the shelves at the store via a commercial vehicle. In fact, national statistics show that nearly 70% of commercial freight activity involves transport by truck. With this much activity, so comes the increased potential of serious accidents involving these vehicles. There are more than 4,000 accidents involving these vehicles every year, nationwide. These accidents result in more than 90,000 injuries per year, and more than 98% of these accidents result in a fatality. Conversely, only 16% of these incidents are found to be the fault of the truck driver.
These commercial vehicles can be broken down by class. There are 8 classes, based upon gross vehicle weight rating (GVWR) of the vehicle. For our use, it is easier to keep them broken into three broad categories:
Light Duty: Commercial vehicles weighing between 6,000 – 14,000 pounds GVWR
Medium Duty: Commercial vehicles weighing between 14,001 – 26,000 pounds GVWR (photo 3)
Heavy Duty: Commercial vehicles weighing more than 26,001 pounds GVWR (photo 4)
There are very little similarities between each truck, as many of them are custom-built for usage as ordered. For example, suspension systems will vary from vehicle to vehicle. While spring suspension systems are considered to be the standard in the industry, there are many different types of systems, including cushion suspension system, Camelback spring systems, air bag systems, and combination spring/air bag systems. They all have one major point to consider, no matter the type of system: each suspension system must be secured by chains to the vehicle, to limit the amount of travel the axles will move when the vehicle is displaced.
Vehicle Hazards
One of the primary hazards rescuers will encounter will be the electrical systems that power the vehicles. The most common system will be the 12-volt system, but it will look much different than the automobile 12-volt system. Commercial vehicles will utilize multiple batteries to provide enough power to turn the engine over and provide voltage for the rest of the vehicle. Batteries will be wired either in Series or Parallel. Series wiring involves sending a path of current through each battery in a single direction. In this case, disconnecting the negative post closest to the frame will break the loop and shut down the electrical system. Parallel wiring involves sending paths of current through each battery concurrently (photo 5). In this case, the rescuer must disconnect all of the negative connections to power down the system. There are also Hybrid Powered Trucks that are on the roads today. Many of these utilize a 60-volt hybrid drive unit in conjunction with the vehicles transmission to drive the vehicle. The unit is powered by a hybrid converter system and can involve well more than 300 volts of electricity. The improvement in vehicle performance shows increases is fuel economy, improved power and performance, and less brake wear as the hybrid unit slows the hydraulic drive of the vehicle’s transmission to assist the braking system. However, be wary of secondary equipment that is installed on the vehicle; there may be a secondary voltage system that powers this unit (photo 6). This power source needs to be secured as well as the main electrical system on the vehicle.
The primary fuel source for these types of vehicles will be diesel fuel, but many other types are still in service. Diesel fuel has four properties that make it popular for use: it is combustible, and provides a more efficient “burn” in the cylinder when it is atomized; it removes heat from the fuel system components; it acts as lubrication for fuel injection parts; and the viscosity of the fuel limits gelling, aiding in flow in colder weather, as long as water can be kept from contaminating the fuel system. Fuel loads for these vehicles do not only sit in saddle tanks on the sides of the vehicle; based upon application, there may be other powered components on the vehicle. For example, tractor trailers that haul perishable goods carry them in refrigerated trailers, or “Reefer Units,” so to speak. These units have a refrigerant system powered by a second engine, and the fuel tank will be found underneath the trailer for this engine (photo 7). Other fuel systems for powered units include road sanders, dolly trailers, and Sani-Vac equipment. No matter the system, the concerns are similar; controlling the flow of fuel is vital. Be sure to shut down the vehicle, keep the fuel shut-off set in the “no-fuel” position, and close all shut off valves on all fuel tanks on the vehicle.
Commercial vehicles utilize pneumatic controls for various devices on the truck. It can be used for climate control settings, wipers, split-shift transmissions, starting systems and suspension/cab ride systems. However, the primary function is the vehicle braking system. Air will be necessary to both release and apply the brakes for the vehicle. There will be a dual air system in these vehicles; the Primary Air System is used for braking, and the Secondary Air System will run other functions on the truck. Keep in mind that if the primary system was to suffer a catastrophic failure (leak), the secondary system will provide enough air to control the braking system for about a minute. After about a minute, as the air exits the vehicle, the brakes will begin to apply by themselves. On the accident scene, it will be necessary to control the pneumatic system. Be sure the parking brake for both the tractor and trailer are applied, chock all wheels where applicable and bleed off all air tanks in both the tractor and the trailer. It is also advisable to disconnect the “glad hands” that provide air delivery to the trailer, and lock them out in a plug bucket type lockout/tagout device (photo 8).
One of the most serious hazards associated with these vehicles are the hydraulic drive systems that operate the truck’s equipment. Hydraulics can be found operating components on trash collection vehicles, cement delivery vehicles, drop deck trailers, lift gates and more. Pressure in these systems can range from 25 psi at idle to upwards of 2,200 psi, based upon the needs of the component. It is critical that these systems are secured and stabilized prior to any extrication operations. Be sure that the vehicle power is shut down, as some of the power for these systems can come from the tractor. Next, block and stabilize the components in place. Do not jog the system or attempt to move the component. Many rescuers will not be familiar with a specific hydraulic component’s controls, and trying to figure it out on-scene has resulted in further injury to the patient, and additional injury to the rescuers.
Next, shut down the hydraulic feed to the system. There will normally be a main shut-off valve somewhere within close proximity of the oil tank. Next, identify any hydraulic components and piping in relation to the extrication. It is very important that rescuers do not cut through any piping during the extrication. Failure of the system may occur, resulting in catastrophic movement of a component, injury from high-pressure atomized oil exposure, and crush injury by being struck with overhead supported loads (photo 9).
Conclusion
One could spend years studying the specifics and designs of commercial vehicles and machinery, but changes in the industry provide new challenges to rescuers every day. Rescuers can benefit by identifying the four potential energy sources listed above, and focus on controlling the potential release of energy that each system holds. Next month, we will be looking at operational considerations on-scene, calculating vehicle and load weight, resources that may be available to aid on-scene and some key hazards that can be found lurking on these vehicles.
Until next time, stay focused and stay safe.
MICHAEL P. DALEY is a lieutenant and training officer with the Monroe Township, NJ, Fire District No. 3, and is an instructor with the Middlesex County Fire Academy, where he is responsible for rescue training curriculum development. Mike has an extensive background in fire service operations and holds degrees in business management and public safety administration. Mike serves as a rescue officer with the New Jersey Urban Search and Rescue Task Force 1 and is a managing member for Fire Service Performance Concepts, a consultant group that provides assistance and support to fire departments with their training programs and course development. Mike has been guest on several Firehouse.com podcasts including: Successful Rescue Operations in Today's Fire Service, Preparing for Tomorrow's RIT Deployment Today and Basement Fire Tactics Roundtable podcasts. View all of Michael's articles and podcasts here. You can reach Michael by e-mail at: [email protected].
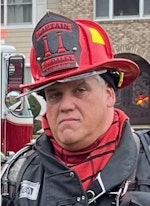
Michael Daley
MICHAEL DALEY, who is a Firehouse contributing editor, recently retired as a 37-year veteran who served as a captain and department training officer in Monroe Township, NJ. He is a staff instructor at multiple New Jersey fire academies and is an adjunct professor in the Fire Science Program at Middlesex County College. Daley is a nationally known instructor who has presented at multiple conferences, including Firehouse Expo and Firehouse World. His education includes accreditations as a Chief Training Officer and a Fire Investigator, and he completed the Craftsman Level of education with Project Kill the Flashover. Daley is a member of the Institution of Fire Engineers and a FEMA Instructor and Rescue Officer with NJ Urban Search and Rescue Task Force 1. He operates Fire Service Performance Concepts, which is a training and research firm that delivers and develops training courses in many fire service competencies.