A motor vehicle accident has occurred at the intersection of a heavily traveled area of a commercial downtown area. It has involved a commercial tanker truck holding about a thousand gallons of diesel fuel, most of which has spilled. The occupants are standing nearby their vehicles and appear shaken. It is a hot, sunny July afternoon with temperatures approaching the 100-degree mark. The sun has baked the asphalt streets and the spilled diesel is pooling against the curb and other low areas. The area of the spill is about 30 feet x 30 feet. The pooled area of fuel is not threatening to spread much beyond its present location, but continues to get deeper. No drains or storm sewers are near the spill, but occupied buildings and spectators are in the area watching your every move, some with video cameras in their phones!
On arrival, the first due company officer has his work cut out for him. First off, the company officer initiates the incident command system, sizes up the situation, calls for the appropriate resources that are and could be needed (being proactive!) and orders the apparatus and crew to take up a position upwind and uphill from the spill. This is an important part of the strategy. While no fuel is presently running downhill and appears to be “pooling,” what happens when the finished foam starts to build up? Could the additional flow cause liquids to run downhill?
Next begins the task of making sure the engine company establishes a sustained water supply. Real quick, our company officer can determine a few critical points as it relates to this incident:
- The spill is a hydrocarbon (diesel fuel)
- It requires an application rate of at least .10 gallons per minute (gpm) per square foot
- The spill is about 30 feet x 30 feet or a total of 900 square feet of fuel
- This requires an application rate of about 90 gpm of foam solution (foam and concentrate mixed at the proper ratio)
- The foam being used in this case is the typical 3% x 6% Alcohol Resistant Aqueous Film Forming Foam (AR-AFFF) concentrate (3% on hydrocarbons and 6% on polar solvents)
- The company has to be able to deliver this flow rate for at least 15 minutes in a worst-case scenario of the spill igniting. For a simple spill, the 15-minute application rate may be overkill, but better to be safe than sorry.
- The company is equipped with a 95 gpm eductor with a 95 gpm air aspirating nozzle, which is above the 90 gpm flow rate required.
- At the 95 gpm rate, the company will be using concentrate metered at 3%. This equates to almost 3 gpm of concentrate and about 92 gallons of water. For 15 minutes this translates into: 45 gallons of concentrate and just less than 1,400 gallons of water
- A backup line that is flowing the same volume would also require a similar amount of concentrate and water. Most forget about the need for a backup line as it relates to foam operations, but like with any building fire, it does offer added protection, an insurance policy of sorts!
The company officer coordinates with the other responding units to set up the foam operation, to mass the needed amount of concentrate and to establish the needed water supplies. These are all important tasks that have to be done quickly and, more importantly, must be done correctly!
The company officer chooses to break the hose lay down into the following setup:
- The apparatus is positioned 200 feet from the spill in an upwind and slightly uphill position and connects to a hydrant
- A 50-foot section of 3-inch line is stretched to the 95 gpm eductor and from the eductor another 200 feet of 1¾-inch hose is attached with a 95 gpm nozzle with a low-expansion, air-aspirating attachment
- Doing the math, we know that the engine pressure should be just over 200 pounds per square inch (psi). This allows for the eductor to receive the necessary 200 psi inlet pressure as there is practically no friction loss in 50 feet of 3-inch hose when flowing only 95 gpm
- After the eductor is positioned, the company officer orders 200 feet of 1¾-inch hose, thus providing enough hose to advance beyond the crash scene if needed
- Of the 200 psi that we are supplying at the eductor, 65% of this can be used for friction loss, elevation (if needed) and for nozzle pressure. Thus, in this case we have 130 PSI as follows:
- 100 psi for nozzle pressure
- 0 psi for elevation loss (actually a slight gain because we are uphill)
- Up to 30 psi to overcome friction loss in the 200 feet of 1¾-inch hose flowing 95 gpm, this is about 22 psi friction loss (depending on the age, maker, and condition of the hose, all determine what the friction loss could actually be. The only sure way to confirm the friction loss in this stretch is to flow test it during training)
- The foam is brought to the eductor’s location and at least 9 x 5 gallon pails are made available, then the attack line has a sufficient amount of concentrate (if each engine carried 5 x 5 gallon pails, a first-alarm assignment could provide a great initial foam-attack capability)
During this preparation phase for foam application, many other tasks can be completed simultaneously, but again, this requires adequate staffing levels, so be proactive and call for assistance early. These other tasks include, but are not limited to, air monitoring, establishment of zones, isolation and denial of entry, identification and confirmation of the product that has spilled and monitoring nearby exposures. Once the logistics associated with the hose stretch and foam staging are complete, the order to charge the line is given. With water flowing at the correct pressure, there are a few things to keep in mind:
- The time for foam to actually be picked up into the stream and delivered to the nozzle (transit time) can be 15 seconds or more, therefore point the nozzle in a direction other than the spill. Once foam is being discharged, then begin the application
- Remember not to plunge the stream into the product, rather bank the stream off the street in front of the spill and allow the finished foam blanket to gently push across the product, creating the required foam barrier that separates the fuel vapor from the air
- The idea of also banking the stream off of a distant object and allowing the finished foam to cascade down and spread out onto the spill is another means of safely applying the finished foam.
- The greater the expansion ratio, the thicker the foam blanket and the longer the “drain time”
- Foam may have to be reapplied as the finished foam blanket begins to break down, so make sure the foam line is at the ready with sufficient amounts of concentrate
- Continue to monitor the surrounding air for an increase in flammable limits. This is an indication that the foam blanket is deteriorating and reapplication is required.
- Check the exposures for a buildup of vapors including the low areas. Full personal protection equipment (PPE) / self-contained breathing apparatus (SCBA) is a must during the recon for explosive mixtures!
- Make sure that the logistics are adequate and enough foam concentrate is available for not only the attack line, but also for a backup line
Problem solving is also a critical part of foam operations. It’s important to remember certain key rules of thumb. If you fail to get foam, try these simple solutions:
- Make sure the inlet pressure is at the correct pressure (usually 200 psi) and then compute that you are not using more than 65% of this number for nozzle pressure, friction loss, and elevation
- Make sure that the nozzle matches or is greater than the eductor in gpm
- Is the nozzle open all the way?
- Are there any kinks in the line that could create additional backpressure?
- Did you allow for enough transit time? Don’t expect finished foam to come out instantly. Transit time could be 15 to 30 seconds!
- Is the eductor pick-up tube more than 6 feet above the concentrate supply?
Other problems could be due to a clogged or blocked eductor or a thick concentrate that is having difficulty being picked up through the strainer on the end of the pick-up tube. To prevent some of the problems associated with clogging, it is critical that the eductor be properly cleaned after each use. As a minimum, the eductor and other appliances in the layout should all be flushed for at least 5 minutes with fresh water after each use. This can pay dividends the next time you go to use it. An ounce of prevention is worth a pound of cure!
Foam Delivery System
Setting up a foam delivery system in your department doesn’t have to be a complex operation. It’s important that every community be able to engage in a basic foam operation. Remember that we are dealing with a variety of fuels ranging from hydrocarbons to polar solvents and a spill or fire involving either should be a part of the department’s preparation.
At the very least, each engine company should have the ability to go into operation and / or support another engine company on scene. To facilitate a more effective foam response, each engine company should be equipped with:
- A 200-psi portable in-line eductor rated at 95 or 120 gpm. (Could a lesser flow work? Absolutely, but strive for overkill in everything you do. There is no such thing as a fair fight!) This doesn’t take up a lot of space, but offers great capability
- A typical fog nozzle rated at 95 gpm or greater, with a low-expansion, air-aspirating attachment that can be snapped on quickly compliments the in-line eductor
- For fuel fires, the standard fog nozzle can deliver a good range, but a lesser expansion ratio (AFFF type foam will work successfully in such an application because aqueous film is being delivered)
- For longer lasting foam (i.e., a higher expansion ratio than the traditional fog nozzle delivers), the air-aspirating attachment offers additional versatility
- The standard 1¾-inch and 2½-inch hose are ideal for typical foam operations. The 2½-inch diameter hose allows for the application of foam from relatively long distances. Remember the numbers associated with the eductor (not more than 65% of the eductor pressure can be used for friction loss, nozzle pressure and elevation)
- Each engine and ladder company should also be provided with 3 to 5 five-gallon pails of foam concentrate. The type depends on the needs of your department, but the AR-AFFF is a great place to start and is of great value on both polar solvent and hydrocarbon fuels. Just make sure you know the manufacturer specifics as it relates to the foam concentrate you are using!
- Finally, these are perishable skills and you must train periodically. Training can be as simple as using “watered-down” foam concentrate (say, 1 gallon per pail and fill the rest with water. This allows members to grasp the principle, see the end result and learn from any mistakes, while operating in a safe, no fire, training setting.
- For those lucky enough to have an actual training area for foam application, use the correct ratios and application rates and make sure a backup line is also available.
This seven-part series covered a lot of material and offers a foundation to build on. But remember, each manufacturer is different and their specific recommendations should be followed as it relates to using their equipment. Also, there are many sources out there that offer significant amounts of information. Take a look at the references identified at the end of the first article in this series. There can be instances of contradiction and confusion if you look at so many sources, but the important thing to remember is to get the specific details as it relates to the equipment you use!
The only way to truly become proficient is through study, training and incident critique. The best time to begin is now, not tomorrow. The fire service is a very in-depth field and countless hours of training, reading and study can bring you to a high level of proficiency, but there is always more to learn. The day you feel you don’t need to pick up a book or to go out and train is the time to hang up your hat!
ARMAND F. GUZZI JR. has been a member of the fire service since 1987. He is a career fire lieutenant with the City of Long Branch, NJ, Fire Department and is the deputy director of the Monmouth County, NJ, Fire Academy where he has taught for over 20 years. He has a masters degree in management and undergraduate degrees in fire science, education, and business administration. View all of Armand's articles here. He can be reached via e-mail at [email protected] or [email protected].
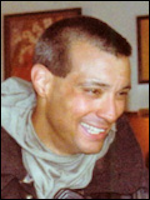
Armand Guzzi | Firehouse.com Contributor
Armand F. Guzzi, Jr. has been a member of the fire service since 1987. He recently retired a career fire lieutenant with the City of Long Branch, NJ, Fire Department and is the deputy director of the Monmouth County, NJ, Fire Academy where he has taught for over 20 years. He has a Master's degree in management and undergraduate degrees in fire science, education, and business administration. View all of Armand's articles here. He can be reached via e-mail at [email protected] or [email protected].