Applying foam is another part of the entire foam strategy that if not done correctly, can lead to injury and property loss. So far, we have talked about developing a foam setup by using the proper types of nozzles, appliances and hoselays. We have discussed the types of concentrate and the necessary application rates, and we have talked about expansion ratios and foam drain time. Now, let’s turn our attention to actually applying the finished foam onto the spill or fire.
We have said it previously in this series and it is so important, that we’ll mention it again. As with any potential for fire, we should always be in the habit of supplying the minimum rate of finished foam. For a spill, a lower flow rate may seem adequate, but what if the fuel did find an ignition source? Get into the habit of applying foam at the minimum application rate for your own safety. If the spill is 300 square feet and this calls for 45 gallons per minute (gpm) of finished foam (.15 gpm per square foot) and you apply 120 gpm, then so be it; the threat will be reduced that much sooner.
Also, another key safety point is the need for a backup line, just in case! We do it at building fires, so why not at a fuel spill or fuel fire?
Once the resources are in place and the necessary amount of foam has been brought to the scene, then it is the time for the application. For our purposes, we’ll talk about the means of applying foam to typical spills and fires that the typical municipal fire department engine company would respond to. What is not a part of this series is the response to the large industrial-type settings or port facilities where specialized fire brigades have access to large types and quantities of specialized foam application equipment. These types of incidents, involving large tanks and significant transportation and handling infrastructure, are well outside the range of this article series.
For the typical engine company, the members should be familiar with three types of methods of foam application. Each is similar in the theory that the fuel spill is disturbed the least. Each method allows for the gentle application of finished foam without causing significant agitation of the fuel. No matter what method is employed, this key facet holds true; the agitation of the fuel or product can create a more volatile situation. Therefore, any of the three methods can offer greater safety and effectiveness during a spill or fire. The three methods are identified with slight variations by different sources and each of the three methods may have different vocabulary, but the principle is the same. Take for example the IFSTA / Brady Essentials of Firefighting (5th Edition) textbook and the Delmar Firefighters Handbook (2nd edition). Both of these texts are of great value to the fire service, but each uses a slightly different vocabulary. The three methods of application, based on these two sources, are as follows:
- The Roll-on Method (IFSTA 5th Edition) and the Bank-in Technique (Delmar 2nd Edition)
- The Bank-down Method (IFSTA 5th Edition) and the Bank-Back Technique (Delmar 2nd Edition)
- The Rain-down Method (IFSTA 5th Edition) and the Rain-down or Snowflake Technique (Delmar 2nd Edition)
The Roll-on Method is a simple concept and allows for the application of foam from a relatively close range. The members stretch a foam line to an area and project a straight stream at the ground with the intention of pushing a foam blanket onto the fuel spill. The power of the stream can easily disturb any spill and splash fuel all over responders, possibly with catastrophic effects. To prevent this debacle, the stream strikes the pavement a few feet shy of the actual spill. In a left to right and back again movement of the nozzle, the nozzle team can push a finished foam blanket farther and farther away from them until the appropriate area is covered.
For even larger spills, the above technique may begin to falter because we can only push the foam so far. The nozzle team can then employ the Bank-down Method. Such a technique uses obstacles farther from the nozzle team. Let’s say a tanker has overturned and there is product between the nozzle team and the overturned tanker. Too great of a distance between the two won’t allow for the Roll-on Method to effectively cover the entire area, so the nozzle team can resort to the Bank-down Method. This entails the foam stream striking the tanker and allowing the finished foam to cascade downward onto the spill and spread out. This is an effective technique and can be used with vehicles, buildings, or any other solid object that won’t fail after being struck. Be wary of electrical components. Foam is mainly water and the nozzle team can be subjected to the danger of electrocution if they’re not careful!
The Rain-down Method is the final of the three techniques for foam application. Like the name implies, a stream is projected high into the air and the finished foam product falls down on top of the product. Moving the nozzle rapidly from side to side will prevent a stream from impacting into the spill.
Regardless of the technique used, remember not to disturb the fuel as best as possible. When the foam blanket is applied it is also important not to disturb the foam blanket as well. The use of a water stream near the foam stream can also have a damaging effect. Plain water will dilute the foam blanket and create an unsafe situation as well as waste the foam that was just applied.
The application of foam requires training and practice. Even just setting up a foam delivery system without using expensive concentrate can offer valuable lessons for firefighters. Concentrate is expensive and slightly corrosive to equipment (requiring five minutes of flushing with fresh water after each use), so it isn’t a drill that we do every day. Nevertheless, we are expected to be proficient in all facets of foam delivery and application.
Putting It All Together
Up to this point, we have covered a lot of material. Now we’ll take a look at how we can apply foam at the site of a spill or fire involving Class B fuels. Everything we do should always be based on safety. The safety of our firefighters, of the civilians we are tasked with safeguarding, as well as other emergency responders on scene all fall within our realm of responsibility.
Our response to an incident requiring foam application requires each responder to conduct his or her own size-up. Size-up is a term that translates into the gathering of clues and vital intelligence that helps orient us towards a safe strategy. Our size-ups are never completed. A size-up is an ever-evolving process on the part of each member. The fireground is a dynamic and ever-changing place. What was appropriate initially may no longer be relevant or even safe! Obviously, the concept of size-up differs significantly depending on the role of the department member.
For example, the newest member of the team, the probationary firefighter, will perform a size-up that might include some of the points that were covered in basic training, such as the class of fire the company will be dealing with, the need to keep a safe distance, and the need for full personal protective equipment (PPE) and self-contained breathing apparatus (SCBA). This size-up differs significantly from that of the first-due company officer. Our company officer has a myriad of tasks going through his mind from the time the call is received to the arrival of the company to the transfer of command to a more experienced officer.
Upon arrival at the scene, some requirements (in addition to the foam operation) also include the need to set up a cohesive command structure. The use of an incident command system (ICS) enhances organizational efficiency and reduces confusion. Our first-due company officer will establish command, break the incident down into manageable bite-size pieces, and establish a staging area to corral the additional units that are arriving. The initial overwhelming burden of so many tasks can be eased by assigning specific objectives to firefighters or assigning tasks to the next-arriving company for example.
As part of the initial size-up, our company officer has to call for the additional resources based on what “could be.” This is proactive thinking and looks at the situation not so much from what is, but what it could be. It is far better to start out additional resources when you think there may be a need than to have to wait for them later. As a company officer, always get into the habit of playing the “what if?” scenario.
Other considerations at the scene of a spill or fire include the need for air monitoring. In addition to applying foam, there is the potential threat of flammable gases finding there way into nearby building and even into below-grade areas. This is an important part of our safety and when enough resources are available, the constant monitoring of the air near the incident should be a standard practice. As we said earlier about intelligence gathering during the size-up, just knowing that there is a potential of fire or explosion enhances our safety. Knowledge is power; it protects us, and this critical intelligence allows us to establish boundaries. The incident we are at is a hazardous materials incident and requires the establishment of zones as well. The hot, warm, and cold zones can be set up as the incident develops, starting with the arrival of the first-due company. Air-monitoring equipment helps to establish the hot, warm, and cold zones that are typical of any hazmat incident.
One important point about air monitoring: make sure your people know how to use their meters! What gas are they calibrated to? How often are they maintained and checked? The use of a meter aids us in our ongoing size-up and it has enormous potential to aid us in our decision-making.
The use of meters should be a constant part of any foam strategy. Even after the foam is applied, it’s important to continually monitor the area. As the foam blanket breaks down, there is the escape of ignitable gases. When the meters detect this, foam needs to be reapplied.
Other tasks that are a requirement include the isolation and evacuation of the area. A spill translates into a potential fire. Take this into account upon arrival. Again, being proactive never hurt anyone!
The tasks and principles described above are all of value to the safety and effectiveness of the fire department response. Nevertheless, the first-alarm assignment may have to do more than perform passive actions. If the situation demands the application of foam at a typical Class B spill or fire involving a hydrocarbon such as gasoline or diesel fuel, then the department has to know their next actions instinctively!
Our actions should always be based on a solid foundation of training. Whether it is for a foam operation or another type of response, we’re only as good as our training has allowed us to be.
In the next, and final, part of this series, we’ll wrap up with a typical scenario and put all the pieces of the puzzle together. We will use everything that we have covered in the past six parts to problem solve in the last article. Until then…
ARMAND F. GUZZI JR. has been a member of the fire service since 1987. He is a career fire lieutenant with the City of Long Branch, NJ, Fire Department and is the deputy director of the Monmouth County, NJ, Fire Academy where he has taught for over 20 years. He has a masters degree in management and undergraduate degrees in fire science, education, and business administration. View all of Armand's articles here. He can be reached via e-mail at: [email protected] or [email protected].
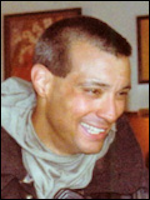
Armand Guzzi | Firehouse.com Contributor
Armand F. Guzzi, Jr. has been a member of the fire service since 1987. He recently retired a career fire lieutenant with the City of Long Branch, NJ, Fire Department and is the deputy director of the Monmouth County, NJ, Fire Academy where he has taught for over 20 years. He has a Master's degree in management and undergraduate degrees in fire science, education, and business administration. View all of Armand's articles here. He can be reached via e-mail at [email protected] or [email protected].