Another important piece in the foam delivery system is understanding the application rates of foam. This is specifically geared towards fuel spills that have ignited. In order to blanket the spill so that the foam blanket is not destroyed from the heat, we have to deliver enough foam at once.
To prevent confusion of various foam related vocabulary, let's take a look some definitions that may cause confusion.
Ratio is meant to describe the amount of concentrate to water. For example, a 3 percent ratio means that we are adding 3 gallons of concentrate and 97 gallons of water to create a foam solution that will be discharged out of the nozzle.
Application rate is the amount of foam solution that must be delivered to a fuel fire to readily extinguish it. The application rate must be able to deliver enough agent to absorb the heat being given off (otherwise the foam blanket will break down) and also provide the smothering effect discussed in previous articles. If the application rate is not delivered, the foam attack may fail and all that concentrate will have been wasted. We'll talk about the logistics associated with the foam attack later on, but for now it is important to understand that any attack must be able to deliver the needed amount of agent over a specific area within a specific time frame. The application rate differs for different types of fuels. This is an important part of the application equation, so know the specifics of your concentrates.
Like structural fire attack, a minimum flow rate is recommended. Even at a spill without fire, it is still highly recommended that the standard application rate be applied. The reason for this is based on our safety. If the spill ignites, we need maximum firepower to control the unexpected! Also, like in structural fire attack, have a backup hoseline in the event you lose foam during the incident. Remember, a backup line should flow equal to or greater than what the attack line flows. This may seem like overkill, but if it prevents one firefighter from being horribly burned and disfigured, then it was worth it!
Duration is the amount of time that the application of foam has to be delivered to create a finished foam blanket that will provide a barrier and prevent reignition. The length of time that this barrier will last before a reapplication is necessary is also dependent on the environment (such as wind), the temperature of the spilled product (hotter fuels will degrade a foam blanket faster), and type of fuel that you are interacting with. NFPA 11 identifies a minimum of a 15-minute application of foam at the required rate as a minimum typical for a spill (IFSTA Principles of Firefighting Foam covers this point in great depth.)
The amount of foam that's required is measured in terms of gallons per minute, per square foot. Each manufacturer has set minimum application rates for specific types of fuels. A good rule of thumb to follow is fires involving hydrocarbons requires between 0.10 gpm/ft2 to 0.15 gpm/ft2 and fires involving polar solvents can range between 0.10 gpm/ft2 0.24 gpm/ft2 . These numbers are very subjective though! Each manufacturer has very specific numbers for certain types of fuels and certain types of foam concentrates. Check the manufacturers web site for the concentrate that your department uses and see the listed application rates.
In addition, each type of foam concentrate has specific ratios with which it has to be mixed with water. You could have a foam concentrate that is rated as a 1 percent x 3 percent AR-AFFF. At 1 percent (1 gallon of concentrate mixing with 99 gallons of water), a major manufacturer's brand says that an application rate of 0.10 gpm/ft2 is required on a hydrocarbon spill, yet this same concentrate can also be used on the polar solvent Ethanol at a 3 percent ratio (3 gallons of concentrate to 97 gallons of water) and requires an application rate also of 0.10 gpm/ft2 .
Training Scenario
Using the requirements we have listed, let's use a simple scenario and see how it all plays out.
The scenario is a fuel spill (a spill is considered less than one inch deep) from a fuel tank on a commercial vehicle. The spill takes up an area of about 30 feet by 30 feet and it has found an ignition source. The fire department incident commander (IC) has determined that the application of foam will be required. Using the data above, the IC considers the following elements: " The spill is a hydrocarbon and requires an application rate of 0.10 gpm/ft2 " The department uses a 3 percent x 6 percent AR-AFFF concentrate, which requires the 3 percent setting for hydrocarbon spills and fires " The area of the spill is 900 square feet " This requires a flow rate of foam solution of no less than 90 gpm " The logistics of such an application rate should be considered for 15 minutes " Based on these minimums, we see that the crews should be able to flow a foam solution through the eductor that consists of almost 3 gallons per minute of concentrate (actually 2.7 gallons), and just over 87 gallons of water per minute (In other words the eductor has its control set at 3 percent.) " For a 15 minute application, this requires about 41 gallons of foam concentrate and about 1,300 gallons of water to maintain the foam application
The exactness of tabletop calculations always goes out the window at the scene of an actually fire or emergency. Our goal is to error on the side of safety and to provide enough agent to safeguard us and the community we are charged with protecting. It pays to have extra resources available for a cushion of safety.
The benefit of the tabletop exercises is that it does give you an idea as to the theoretical details required. So long as you have a working knowledge of the concepts, you'll be able to apply the theories with some degree of accuracy even during the extreme stress of the emergency. Will it be perfect? Probably not, but if you error on the side of caution it may prove to be overkill and that's great!
Foam Expansion Ratios
So far in this series we have covered many elements of the foam delivery system. Now we'll bring our studies to the actual working end of the foam stream. The delivery of foam requires that each step in the process be understood and that certain key points be adhered to.
We have talked about the three primary ingredients that comprise finished foam: air, water, and concentrate. We know that water is delivered via a hoseline and foam concentrate is inducted into the hoseline via an eductor. This foam solution then makes its way to the end of the line where we find our nozzle. The proper nozzle is a key part in the delivery process.
As foam solution is discharged from the nozzle, the agitation of the stream with the air causes air to mix and become entrained with the stream of foam solution. In other words the foam/water solution now mixed with air is discharged as finished foam.
Finished foam has various expansion ratios. Expansion ratio is the amount of air that is mixed with the foam solution. For example, a 10:1 ratio simply means that 10 parts of air is mixed with 1 part of foam solution. If the nozzle is delivering a 125-gallon per minute foam solution stream and then is mixed at a 10:1 ratio with air, we ultimately have 1,250 gallons of finished foam. Obviously this large amount of foam is 90 percent air. Nevertheless, air is a key component of finished foam and helps to orient us towards a particular strategy.
Expansion ratios range from low expansion (up to 20 parts air to 1 part foam solution), to medium expansion (up to 200 parts of air to 1 part foam solution), to high expansion foam where up to 1,000 parts of air are delivered to 1 part foam solution.
Each expansion ratio has its own purpose and no one expansion ratio is better than another. Each is a tool in the toolbox and has its own purpose. For example, high expansion foam is delivered via a special delivery system that requires a fan similar in appearance to a smoke ejector to force air into a foam stream. The end result is a very thick blanket that can be used to smother a hidden fire in a hard to reach areas, such as a basement. The use of high expansion foam is out of the realm of this article, but it is another tool for the incident commander should he or she have access to such a resource. High expansion foam has been used successfully in the past to extinguish or at least, control, fires in very difficult to reach spaces such as a cellar or sub-cellar.
A fire in a cellar is primarily a Class A fire and the purpose of high expansion foam will be to smother the fire and reduce its intensity. High expansion foam must be delivered relatively close to an entry point. Because it consists of so much air that a good breeze could blow it away. Placing the foam delivery system near an opening, such as a Bilko door to the basement, also requires a vent point opposite this location. High expansion foam can be hindered from moving very easily because it is so fragile. A vent point opposite the delivery point will allow the foam to flow naturally and smother the main fire.
For final extinguishment, the application of hoselines is required, but the value of the high expansion foam can be seen. It is a special category that is an area of specialization unto itself. Again, consult the major manufacturers and some of today's exceptional fire service authors for specifics on working with high expansion foam. For our purposes, the reason for explaining high expansion foam is to present the reader with a sense of expansion ratios at the upper end of the spectrum. This is certainly not a typical tactic for today's fire service.
Medium expansion foam (up to 200:1) can be delivered via a specialized nozzle. It is not as dependent on wind conditions as high expansion foam, but the foam stream range is limited. Again, most of the stream is air and subjected to various limitations. Medium expansion foam is not a common application for the typical municipal fire department.
Low expansion foam has an air to foam solution ratio of up to 20:1. This offer a longer reaching stream and greater penetration of a thermal column. A foam blanket can be created successfully, but not with the same degree of thickness as would be experienced with medium expansion foam. Therefore the advantages and limitations of each application must be weighed with the situation at hand.
Nozzles And Air Aspiration
Most municipal foam operations are centered on low expansion foam applications. Nozzles can be divided into two primary categories, air aspirating and non-air aspirating.
Non air-aspirating nozzles are the typical fog nozzles used on our engine companies today. These nozzles can effectively apply an Aqueous Film Forming Foam (AFFF) or a Film Forming Fluoroprotein (FFFP) Foam solution at an expansion ratio of really no more than 6 or 7:1 depending on the manufacturer, and as low as 2:1. Set on a straight stream, the nozzle will deliver the greatest range of finished foam. This increase in range enhances the safety of our members as well. In addition, the straight stream setting offers the greatest expansion ratio compared to a wider fog pattern because the stream is initially impinging on itself as it leaves the nozzle. This agitation is a critical component of foam application and as such, the typical fire department fog nozzle offers great value and flexibility.
The non-air aspirating nozzle can be of great value for the typical hydrocarbon spill because of the aqueous film solution that is part of the finished foam. This film moves out quickly ahead of the main foam blanket and begins to cover the spill. The use of the non-air aspirating nozzle is of limited value on polar solvents. For these incidents, an air-aspirating nozzle allows the polymeric membrane to form and create the necessary barrier.
Air-aspirating nozzles are a more specialized nozzle that is designed to entrain air into the stream at a higher ratio than a typical fog nozzle. The types of air aspirating nozzles vary and are designed to flow various quantities of finished foam depending on the model. Air aspirating nozzles come in basically two varieties. The first is an attachment for the typical fog nozzle. This is an easy way to acquire a thicker finished foam blanket. The expansion ratio varies but a 10:1 expansion ratio is a good number to start at. Consult the various manufacturers for the specific details of these air aspirating nozzle attachments. They offer a shorter range but provide a better expansion ratio than the typical fog nozzle without such an attachment.
The second variety of air aspirating nozzle is specifically designed for foam application. These tube like nozzles induct air into the stream at about a 10:1 ratio or better. The range of the stream is fair and the expansion ratio is also better than any fog nozzle alone.
The application of foam via an air aspirating or non air-aspirating nozzle depends on the type of spill. For example, the use of an air-aspirating nozzle can be successfully used to apply finished foam to both polar solvents as well as hydrocarbons. But, the application of foam via a non air-aspirating nozzle can primarily be successful on hydrocarbon spills. These nozzles allow for the aqueous film to spread rapidly onto the spill but the membrane that would be needed for use on a polar solvent requires the air aspirating type of nozzle.
In addition, a low expansion application results in a shorter drain time which means that due to limited agitation, the foam blanket is not as thick and will not last as long. The finished foam will be much wetter in a low expansion application, especially when applied through a traditional fog nozzle. As we said earlier, this does have certain advantages such as the ability to penetrate a heated thermal column. The finished foam is also less prone to be affected by wind, and the finished foam will spread out more rapidly on the spill surface.
A disadvantage of such low expansion foam is its rapid drain time. When the foam blanket begins to break down, it becomes vulnerable to ignitable vapors mixing with air. Air monitoring should be an ever-present concern around the entire area to include the monitoring within exposure buildings for any flammable gas buildup. Remain on the alert even after the foam blanket has been applied as any break in the seal could result in a rapidly ignited fire.
Quite the opposite can be said of medium to high expansion foams. A thick blanket of foam will have a longer drain time, but can be affected adversely by wind and even by the intensity of the fire.
Regardless of the type of finished foam used, if the fuel is very hot, there is the danger that the foam blanket could be degraded quickly. Since foam is primarily water, it does offer a cooling ability but in order to achieve this cooling, requires large applications of finished foam.
As with any foam operation, it is important that the nozzle match the eductor being used. Never should the nozzle be of a lower flow capability than the eductor. The nozzle should, as a minimum, be of the same flow or higher than the eductor. Lets take a look at an example that requires the application of foam via a typical adjustable gallonage fog nozzle.
A great advantage of knowing the math behind the foam process allows for even greater flexibility. Take the basics of what we have covered so far in the series. In this example let's use a 95-gpm eductor with a 200 psi rated inlet pressure. We know that our rule of thumb is that 65 percent of this number (130 psi) can be used for nozzle pressure, friction loss, and elevation. On the discharge end of the eductor we have 1 3/4-inch hose on level grade to a 100 psi adjustable gallonage nozzle that must be set on 95 gpm as a minimum.
The gallonage ring on the nozzle goes up to 125 gpm, then to 150 gpm and finally, the highest flow setting is 200 gpm. We must have a nozzle that flows the same amount as the eductor as a minimum. But what if we had the nozzle set on a higher flow than 95 gpm? The eductor will still flow the same amount of solution simply because the eductor is receiving the 200 psi inlet pressure. This allows us a lot more versatility and we can now conduct foam operations at a higher elevation or with a longer stretch of hose. Let me explain...
If we move the gallonage ring to 125 gpm, the nozzle will still flow 95 gpm of foam solution and offer finished foam at a low expansion ratio, but the nozzle pressure will only be 58 psi. This allows us to use the extra energy that was allotted to nozzle pressure to now be used for either friction loss or elevation.
In other words: " We have a total of 130 psi to use for friction loss, elevation, and nozzle pressure " Flowing 95 gpm through an orifice sized to flow 125 gpm requires a nozzle pressure of 58 psi " Taking the 130 psi (this is 65 percent of the 200 psi eductor inlet pressure that we cannot exceed) and subtracting the nozzle pressure of 58 psi, gives us 72 psi for friction loss and elevation " If the stretch was 200 feet of 1 3/4-inch hose, this has a friction loss of about 10 psi per hundred feet or a total loss of 20 psi " We now have a remaining 52-psi to overcome elevation, for say, a fire on the upper floor of a parking garage for example. At 5 psi per floor above the first, we can go over a hundred feet high!
Successful foam operations mean being able to interpret these numbers and come up with a solution to any specific emergency. For an eductor to work properly it must not experience too much backpressure. If it does, the foam will not be inducted into the pickup tube and we will not flow any foam!
Just remember, the key is no more than 65 percent of the eductor inlet pressure that can be allotted for nozzle pressure, elevation, and friction loss. Thus a 200-psi eductor can give you the flexibility of using up to 130 psi anyway you see fit.
Low expansion foam is the typical application used by municipal fire departments. It can be applied via an air aspirating or non-air aspirating nozzle and can be applied at more standard nozzle pressures such as 100 psi, but can also be applied at even lower nozzle pressures. The expansion ratio will be affected at these lower pressures though. The reason for this lower expansion ratio is there is less pressure (or energy) to create the agitation necessary to mix the foam solution with the air.
Nevertheless, foams that create an aqueous film can be applied successfully on hydrocarbon spills and fires. These foam blankets will not last as long as a thicker and richer foam blanket, such as one applied at a higher ratio, but it will offer the knockdown power that can be the difference between a major incident or a more mundane one.
As with all of the tools we rely on in the fire service, there are advantages and disadvantages of low expansion foam. Until next time, take a look at your department and see if you can answer these questions: " What are your eductors rated at? " What nozzle pressures do your fog nozzles operate at? Are they automatic nozzles or of an adjustable gallonage type? " Do you have any special purpose air-aspirating foam attachments that clip on to your fog nozzles? Do you know how they work? " What are the application rates for the foam concentrates your department uses? You may have to consult the various manufacturers' websites for the specifics, but now is the time to find out!
ARMAND F. GUZZI JR. has been a member of the fire service since 1987. He is a career fire lieutenant with the City of Long Branch, NJ, Fire Department and is the deputy director of the Monmouth County, NJ, Fire Academy where he has taught for over 20 years. He has a masters degree in management and undergraduate degrees in fire science, education, and business administration. View all of Armand's articles here. He can be reached via e-mail at[email protected] or [email protected].
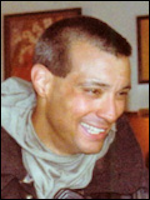
Armand Guzzi | Firehouse.com Contributor
Armand F. Guzzi, Jr. has been a member of the fire service since 1987. He recently retired a career fire lieutenant with the City of Long Branch, NJ, Fire Department and is the deputy director of the Monmouth County, NJ, Fire Academy where he has taught for over 20 years. He has a Master's degree in management and undergraduate degrees in fire science, education, and business administration. View all of Armand's articles here. He can be reached via e-mail at [email protected] or [email protected].