Up to this point, we have covered a lot of valuable points. The proper proportioning of foam concentrate is another critical piece in the foam application process. Our goal is to mix the foam concentrate with the water in the proper ratio so that after it leaves the nozzles and is mixed further with air, it will offer a protective barrier that will separate the fuel vapors from the air.
There are several ways for this mixing to occur. For the purposes of this series, we’ll simply concentrate on the inline portable eductor. The inline portable eductor is a very simple appliance that allows any engine company to engage in a simple foam operation. An eductor works on the Venturi principle, whereby the appliance (the eductor) picks up concentrate and adds it directly to the hose stream without water diverting from its intended course. Eductors have various ratings of how much foam solution they flow at the proper pressure. For example, some of the more common flows are 60, 95, 125, and 250 gallons per minute (GPM). This is a mix of both water and concentrate at the proper ratio.
For example, if a 125 GPM eductor is in operation with the required pressure and 3% foam concentrate is being used, then the foam solution mixture will consist of approximately 3.75 GPM of concentrate and just over 121 GPM of water.
The portable inline eductor offers quite a punch to the engine company’s arsenal. We have the ability to flow for small spills and fires right on up to the larger incidents we could typically encounter. For even larger incidents, nozzle-mounted eductors can be used to deliver even larger quantities of foam solution. With the nozzle eductor, there is less maneuverability, but much greater punch. For our purposes, we’ll stick with covering the simple portable inline eductor.
The inline eductor is placed somewhere in the hoseline layout, hence the name “inline” eductor. It could be attached to a discharge on the side of the engine company or could even be installed between two couplings as part of a longer hose layout. The option for acquiring a foam stream from a lengthy distance away is possible, so long as the principle of this appliance is understood.
They say that where the eductor goes, so goes the foam supply. Foam concentrate in five-gallon pails, for example, are brought to the point where the eductor is. The “pick-up” tube of the eductor is placed into the foam supply and, at the proper inlet pressure to the eductor, the foam concentrate is pushed (via atmospheric pressure) up the pick-up tube and added into the water stream. Each eductor has a check valve to prevent water from back flowing into the foam supply.
Many departments place the pick-up tube into the five-gallon foam pail. With the higher rates of proportioning, the pick-up tube has to be placed into a new foam pail every few moments. For example, a 250 GPM foam stream at 6% would mean 15 gallons of concentrate every minute. This is a five-gallon pail every 20 seconds. The firefighter assigned to the foam supply at the eductor has to pay careful attention to ensure a continuous foam supply. The last thing the nozzle team would want to experience is a loss of foam. The danger of diluting the foam blanket would be a very real threat.
Rather than this tedious process of a firefighter moving the pick-up tube every so often, try using a container such as a wash bin or other open top vessel that holds 20 or 30 gallons. The logistics of this is a relatively simple concept…keep the pick-up tube in the metal wash basin and keep adding pail after pail after pail. A steady supply of foam is readily available and visible, and with a bit of common sense, no concentrate will overflow the basin.
Each eductor has a manual control or metering valve that varies the orifice size to take in foam concentrate. The metering valve has a series of numbers on it such as 1%, 3%, and 6 %. Some of the newer portable inline eductors have percentage settings that are even lower, such as ¼ or ½ of a percent. These smaller fractions of 1% are for use with Class A foam concentrates and allow for a more versatile engine company.
It’s important that the metering valve be set at the correct percentage setting otherwise the ratio of concentrate to water may be too lean. If the department plans on using a 3% mix (3 gallons of concentrate to 97 gallons of water), then the metering valve should be set appropriately. Failure to match this setting with what a particular spill calls for could result in a weak foam blanket and a potentially unsafe situation. Therefore, always make sure that the eductor is set on the proper ratio for the situation.
Don’t confuse the setting of the metering valve with the amount of foam solution it flows. For example, a foam eductor may be rated at 250 gallons per minute (GPM), with an inlet pressure of 200 pounds per square inch (PSI). The metering valve is then set for any of several settings such as 1%, 3% or 6%, for example. In other words, using this eductor can have a flow range of 2.5 gallons of concentrate and 247.5 gallons of water per minute with the metering valve set at 1%. With the control set at 3%, the foam solution ratio is 7.5 gallons of concentrate and 242.5 gallons of water per minute. Finally, with the valve set at 6%, we get 15 gallons of concentrate mixed with 235 gallons of water per minute.
If an eductor receives less than the correct inlet pressure, let’s say 150 PSI instead of 200 PSI, the foam solution will be “richer” in concentrate. If the eductor had an inlet pressure of say, 225 PSI instead of 200 PSI, then the foam stream would be too lean. Foam that is too lean doesn’t create the proper application it’s designed to and this can create a weak foam blanket.
One important note about picking up foam concentrate and adding into the stream; the pick-up tube should be no more than six feet above the surface of the concentrate. Beyond this height, no foam concentrate will be picked up, or at the very least, certainly not the proper ratio.
Also, both the alcohol resistant Aqueous Film Forming Foam (AFFF) and alcohol resistant Film Forming Fluoroprotein (FFFP) are a thicker concentrate than non-alcohol resistant concentrates. This greater viscosity requires more effort to pickup. Colder temperatures can also affect viscosity. All UL-approved foam concentrates are proportion tested to as low as 35 degrees. Some manufacturers offer a pickup with a slightly larger diameter and some sources recommend that the small strainer at the end of the pickup tube be removed to aid in concentrate pickup and delivery.
The inlet pressure of the eductor varies with the manufacturer, but most operate at an inlet pressure of 200 PSI. The next bit of information will determine if your foam streams are successful or not. Backpressure becomes a serious issue with foam operations and the portable inline eductor. With a 200 PSI inlet pressure, the engine company cannot exceed 65% of this number for nozzle pressure, friction loss, and elevation loss on the discharge side of the eductor.
As an example, suppose we have a small fire and are tasked with going into action with our foam eductor. The eductor has an inlet pressure of 200 PSI. We know that 65% of this, or 130 PSI, can be allotted for hose, appliances, and elevation. If the nozzle has an operating pressure of 100 PSI, we have only 30 PSI remaining for use in friction loss and/or elevation loss.
Let’s say that the nozzle in this scenario is level with the eductor and therefore elevation is not an issue in this stretch. That gives us 30 PSI remaining for overcoming friction loss. If the eductor is designed to flow 125 GPM and we are using 1¾” hose, then the friction loss in this hose at 125 GPM is about 20 PSI per hundred feet. Therefore, we can stretch a line as long as 150 feet of 1¾” hose to apply the foam stream.
Let’s take a look at that again, here are the highlights:
- We are using a 125 GPM eductor with a rated inlet pressure of 200 PSI
- We can allot no more than 130 PSI for elevation, friction loss, and nozzle pressure (65% of the rated eductor inlet pressure)
- Friction loss in 150 feet of 1¾” hose at 125 GPM is about 30 PSI (maybe more or less depending on the brand of hose, age, and wear on it)
- Nozzle pressure is 100 PSI in this scenario
- Elevation is zero in this scenario
- Therefore we can stretch no more than 150 feet of 1¾” hose with a 100 PSI nozzle from the eductor to the scene
Depending on the quantity of solution flowing, the length and diameter of the hoseline being used, the nozzle pressure required, and the elevation, all together determine just how far you can stretch a line. The key is not exceeding the 65% of the rated inlet pressure. Remember, as with any appliance, each manufacturer has their own rules and guidelines, so make sure you know the specific details of your own equipment. Take a look at the individual specifications of your equipment. The web sites at the end of the first part in this series have a lot of detail that can guide you in your fireground decision-making.
A valuable attribute of the portable eductor is that it can be placed closer to the scene in situations that preclude the engine from getting close. Take for example a fire at a dock of private yachts and vessels. A fuel leak has ignited and multiple small boats are presenting an exposure problem. The fuel is burning on the surface of the water. The engine stops 500 feet from the fire and is unable to get any closer. This is certainly too far to use 1¾” hose to get a foam line in operation, so what can we do?
- The engine stretches 400 feet of 3” hose (with 2½” couplings) to a 2 ½” x 1½”reducer
- Then a portable eductor with 1½” threads is placed in the stretch
- From the eductor another 150’ of 1¾” is stretched with the appropriate nozzle
- The engine discharge pressure is about 210 PSI (the 10 PSI compensates for the friction loss in the 3” hose going to the eductor)
- The eductor now has an inlet pressure of 200 PSI
- The eductor we’re using in this scenario is rated at 125 GPM
- Foam solution is then delivered via the 1¾” hose line to the vessel on fire
As you can see, the portable eductor has a lot of versatility. It is a relatively inexpensive and effective way to get a basic foam line into operation.
This is just one scenario for the use of the portable eductor. We’ll use more scenario-based examples as the articles continue, but this gives the reader an idea of the opportunities we have to get a foam line in operation a lengthy distance from the engine company. Remember though, where the eductor is set up is also where the foam concentrate has to be delivered. This requires the necessary logistics.
Until next time we meet, take a look at your portable inline eductors and see if you can answer these simple questions:
- What is the eductor rated at? 60 GPM? 95 GPM? 125 GPM?
- What is the required inlet pressure? 200 PSI? Less than 200 PSI?
- What percentage does the metering valve have listed on it? 1%, 3%, 6%?
- Does the end of the pick-up tube have a small screen on it or not?
ARMAND F. GUZZI JR. has been a member of the fire service since 1987. He is a career fire lieutenant with the City of Long Branch, NJ, Fire Department and is the deputy director of the Monmouth County, NJ, Fire Academy where he has taught for over 20 years. He has a masters degree in management and undergraduate degrees in fire science, education, and business administration. View all of Armand's articles here. He can be reached via e-mail at [email protected] or [email protected].
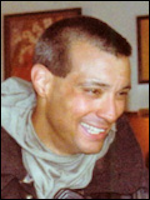
Armand Guzzi | Firehouse.com Contributor
Armand F. Guzzi, Jr. has been a member of the fire service since 1987. He recently retired a career fire lieutenant with the City of Long Branch, NJ, Fire Department and is the deputy director of the Monmouth County, NJ, Fire Academy where he has taught for over 20 years. He has a Master's degree in management and undergraduate degrees in fire science, education, and business administration. View all of Armand's articles here. He can be reached via e-mail at [email protected] or [email protected].