Ethanol (ethyl alcohol) is the alcohol used to create beer, wine and other alcoholic beverages. Ethanol is also produced as an alternative fuel to gasoline. In the U.S., more than 9 billion gallons of ethanol fuel is produced annually. Ethanol is typically produced from corn or sugarcane. The U.S. is the world's largest producer of ethanol and primarily uses corn. Ethanol fuel has a few disadvantages; it has a lower energy density than gasoline, so a tank of ethanol fuel will not go as far as a tank of gasoline, and ethanol fuel can be more difficult to start in very cold temperatures.
Ethanol fuel is also used as an oxygenate additive to gasoline. In the past, the chemical methyl tert-butyl ether (MTBE) was used for this purpose, but MTBE is hazardous and harmful to the environment. Ethanol fuel can provide the same function without its negative effects to the environment. Oxygenating gasoline boosts the octane quality, enhances combustion and reduces carbon monoxide (CO) emissions.
The Nebraska community of Fairmont is home to Advanced Bio Energy's ethanol facility, which produces 110 million gallons of ethanol from corn each year. As a byproduct of ethanol production, the plant also produces 320,000 tons of Distiller's Dried Grains with Solubles (DDGS) each year. DDGS is a high-value livestock feed primarily for cattle, but also used for poultry and hogs. Three pounds of corn produces one pound of alcohol, one pound of carbon dioxide (CO2), released into the atmosphere, and one pound of distiller's grain.
Advanced Bio Energy's Fairmont Ethanol Plant sits on 260 acres just west of the village of Fairmont and began operations in October 2007. The plant operates with 42 employees 24/7, 365 days a year with 10 days of scheduled down time for maintenance. Fairmont is a community of 691 residents, according to the 2000 census, at the intersection of U.S. Highways 6 and 81 with Interstate 80 just 15 minutes to the north. The facility is in the heart of Nebraska corn country, with a large percentage of irrigated crops to counter the effects of drought. This location allows for continued maintenance of the corn supply needed to operate the plant.
Fairmont has an all-volunteer fire department with about 30 members under the leadership of Chief Bobby Hoeft, Assistant/Deputy Chief Jeff Neiman and Assistant Chief Lonnie Taylor. The Fairmont Volunteer Fire Department operates one pumper, two tankers, a brush/rescue truck and an ambulance. A new tanker was delivered in late 2009 and a new pumper will be delivered in the spring of 2010.
Ethanol plants, whether in Nebraska or any other state, vary in size, but the process of producing ethanol from corn is much the same. If you were to visit more than one ethanol plant, you would find them similar in layout and the equipment used to produce ethanol. I was most impressed by the safety features built into the facility and the safety attitude of the employees. Additionally, the plant was very clean. Cleanliness is necessary for the fermentation process to work properly. The entire facility is sprinklered and it has its own 3,500-gpm fire pump, half-million-gallon water storage tank, foam monitors, hydrants and foam supply. Advanced Bio Energy does not have a fire brigade of its own and relies totally on the Fairmont Volunteer Fire Department and other local volunteer fire departments through mutual aid for fire protection and other emergency responses.
Ethanol production begins with the delivery of the raw material — corn — to the facility. Much of it is trucked in from local producers. The day I visited the Fairmont facility, 18-wheelers were lined up for several blocks to empty their loads of corn into the enclosed receiving area at the plant. This same facility is used to load and ship the distiller's grain. Raw grain is trucked into the facility and distiller's grain is shipped from the facility by rail.
The transfer and storage of grain at the ethanol plant is like any other grain elevator operation — there is the potential for dust explosion from the grain dust. Grain is dumped into a collection pit and transferred into the storage bins at the facility. Dust-control equipment is in place to reduce the chances of dust explosions. The elevator has an external leg that is equipped with explosion venting. The leg transfers the grain to and from the storage silos. Stored grain generally contains two to 10 pounds of grain dust per ton.
Ethanol is a flammable liquid, according to the U.S. Department of Transportation (DOT). It is shipped under the red flammable liquid placard with the United Nations four-digit identification number 1987, which is used for all alcohols. Other hazardous materials located at a typical ethanol plant include anhydrous ammonia (NH3), sulfuric acid, phosphoric acid, ferric chloride and sulphamic acid (for cleaning tanks). Welding gases are also present in maintenance shop areas.
Anhydrous ammonia and sulfuric acid are trucked into the plant twice weekly and stored in large tanks outside the plant. They are piped inside the facility for use in the ethanol production process. Anhydrous ammonia is a toxic corrosive gas, which is also flammable, especially when inside of a facility or an enclosed area. It is classified by the DOT as a non-flammable gas because it does not meet the DOT definition of flammable gas. Anhydrous ammonia is classified as a 2.3 toxic gas under the United Nations Hazard Class System. The National Fire Protection Association (NFPA) 704 standard classifies anhydrous ammonia as Health Hazard 3, Flammability 1 and Reactivity 0. The important points to remember about anhydrous ammonia are its toxicity and flammability since it is piped into the ethanol production facility. A leak inside the plant could result in an explosion or fire if it encounters an ignition source. Contact with the skin, particularly if the skin is moist, will cause severe burns. Contact with the eyes can cause blindness. The word anhydrous means without water. As a result, anhydrous ammonia seeks water and will affect moist areas of the body.
Sulfuric acid is corrosive and toxic and one of the top industrial chemicals in terms of total production quantity in the U.S. The DOT classifies sulfuric acid as a Class 8 Corrosive Liquid. Phosphoric acid is also a Class 8 Corrosive Liquid. Both sulfuric and phosphoric acids are listed under the NFPA 704 classification system as Health Hazard 3, Flammable Hazard 0 and Reactivity Hazard 2. They cause severe burns in contact with skin. Ferric chloride is corrosive and can cause burns on skin contact. It is listed by NFPA 704 as Health Hazard 3, Flammability 0 and Reactivity 2. The DOT classifies ferric chloride as a Class 8 corrosive solid. Sulphamic acid is corrosive and can cause burns in contact with skin. It is classified the same as ferric chloride.
Production of ethanol begins by extracting starch from the corn. Corn is moved into the process facility on a conveyor and placed into tanks. Enzymes are used to extract the starch from the corn and it is turned into sugar. Yeast is then mixed into the sugar in 8,000-gallon fermentation tanks. It is the fermentation process that ultimately produces ethanol. Fermentation creates heat and circulating water is used to cool the process to 91 degrees Fahrenheit for the yeast to work properly. Sulfuric acid is used to clean equipment and adjusting the pH for optimum fermentation. Anhydrous ammonia is used for pH correction and supplies nutrients for the yeast.
When the process is finished, 200-proof ethanol is produced. It is then denatured with 2.5% natural gasoline produced from natural gas. Denaturing is done to prevent the ethanol from being used as drinking alcohol. The finished product is 190 proof and is stored in 200,000-gallon closed floating roof tanks at the facility. Production capacity at the Fairmont plant is 3 million gallons and there are usually 1 million gallons on hand. Ethanol produced at Fairmont is shipped by rail to Dallas/Fort Worth, TX, and California. There are 96 to 112 rail cars on site at any given time, each with a capacity of 30,000 gallons of ethanol. Railcars are filled at a specially designed loading rack. The rail car loading rack is protected by a 750-gpm deluge system in the event of a fire during the loading process.
Piping in the plant is painted to indicate what is in the pipes. Yellow pipes carry chemicals, red pipes are 120-psi steam, silver pipes are process lines with 185° F liquids and green pipes carry clean water. Leaking or ruptured pipes can be hazardous to emergency responders, so caution should be exercised in response to leaks. Floor grates are located throughout the process area with sump pumps to route ethanol spills back into the process. Dryers in the Energy Center building that are used to dry grain are powered by natural gas and produce temperatures of 800° to 900° F during normal operations. Thermal oxidizers in the same building produce temperatures up to 1,600° F. Thermal oxidizers are used to burn off exhaust from the drying process to prevent odor. Steam is also a byproduct of the thermal oxidizer process. CO2 and heat are only byproducts of the ethanol plant operation that are released into the atmosphere. Production of ethanol produces approximately 21% less CO2 than the production of gasoline.
Emergency responders with ethanol plants in their jurisdictions may want to become acquainted with management and safety personnel at the plants. Knowledge of the characteristics of ethanol and other hazardous materials at the facility could also be helpful. Learn the plant layout and type of fire protection equipment available. Understand the production process for ethanol and know where hazardous materials and areas are located at the facility. Proper knowledge and pre-planning of the facility can make responding to an emergency safer and more efficient.
Thanks to Bridget Smale of Advanced Bio Energy corporate office, Fairmont Plant Manager Grant Johanson and Fairmont Plant Safety Officer Megan Williams for their assistance in making the plant tour possible and during the tour itself.
ROBERT BURKE, a Firehouse® contributing editor, is the fire marshal for the University of Maryland Baltimore. He is a Certified Fire Protection Specialist (CFSP), Fire Inspector II, Fire Inspector III, Fire Investigator and Hazardous Materials Specialist, and has served on state and county hazardous materials response teams. Burke is an adjunct instructor at the National Fire Academy and the Community College of Baltimore, Catonsville Campus, and the author of the textbooks Hazardous Materials Chemistry for Emergency Responders and Counter-Terrorism for Emergency Responders. He can be contacted at [email protected].
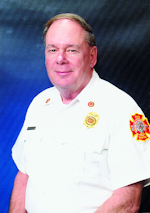
Robert Burke
Robert Burke, who is a hazardous materials and fire protection consultant and who served as a Firehouse contributing editor, is a Certified Fire Protection Specialist (CFSP), Fire Inspector II, Fire Inspector III, Fire Investigator and Hazardous Materials Specialist. He has served on state and county hazmat teams. Burke is the author of the textbooks "Hazardous Materials Chemistry for Emergency Responders," "Counter-Terrorism for Emergency Responders," "Fire Protection: Systems and Response," "Hazmat Teams Across America" and "Hazmatology: The Science of Hazardous Materials."