SUBJECT: Advanced Steel
TOPIC: Extrication Challenges of Advanced Steel in Vehicles: Part 4
OBJECTIVE: The rescuer will understand and explain the capabilities and limitations of various hydraulic-powered rescue cutter tools
TASK: Given the information presented in Part 4 of this series, the rescuer will demonstrate the steps necessary to effectively operate a power cutter to cut through the advanced steel structural areas of a late-model passenger vehicle.
As a rescuer, just having a hydraulic-powered cutter unit in your tool inventory no longer guarantees that you will be able to cut through all the structural areas of a crash-damaged passenger vehicle. There may be nothing mechanically wrong with the tool you are using; it probably worked hundreds of times before to do the same thing you are trying to do now. Your failure may simply be a matter of your cutter being outgunned by the strength of the ultra-high-strength advanced steels found in new vehicles.
In Part 4, we look at research being conducted with hydraulic-powered cutters to determine what it takes to cut the advanced steels and how cutters can best be used to complete this task. The pioneering research by this author has revealed some new and interesting information about the challenge of new vehicle extrication. Also, it has become apparent that not only the power of the cutter but other factors such as tool positioning, hose length, pump fluid flows as well as the blade design itself can mean the difference between making the cut or not.
The hydraulic rescue tool manufacturers are all acutely aware of the challenge of cutting advanced steel. All rescue tool manufacturers have cutters that will not cut through advanced steels; that is obvious. They are typically a cutter manufactured in the 1980s, '90s or the past few years. Generally, it will be a newer model cutter that is capable of cutting through the advanced steels such as Boron.
A field research project was designed and put into action by this author. Power rescue cutters are being assigned standardized tasks consisting of cutting through vehicle A-pillars, roof rails and B-pillars that are known to contain advanced steels. To create consistency and a level playing field, the project required lots of exactly the same type and thickness of advanced steel to cut through. The steel engineers from the American Iron & Steel Institute in Southfield, MI, provided technical data on the exact composition of the advanced steels used in our test vehicles. In a cooperative effort with officials at the Vehicle Research Center of State Farm Insurance, several crash-damaged late-model vehicles were provided from their "total loss" inventory. These vehicles all had exactly the same Boron structural steel design.
Systematically, each rescue tool manufacturer has been offered the opportunity to submit various makes and models of power cutters to be put through the testing. Each cutter is used to cut "thin" Boron; in this case, metal that was slightly thicker than a dime. The roof rails of the donated vehicles all had 0.889-millimeter-thick Boron, so that was our thin testing. For the "thick" Boron test, each cutter had to cut through the B-pillar at a point where the Boron was known to be 1.9 millimeters thick and was wrapped inside multiple layers of mild steel. This Boron was thicker than a quarter.
Lessons Learned
Results have shown cutter failures and successes. Some of the lessons learned:
- The ability of a power cutter to get through the Boron testing did not necessarily correspond with each manufacturer's published cutting forces for its tool. In other words, just having an advertised big-number cutting force rating for a specific tool did not guarantee that Boron could be cut in our tests. It seems that the ratings of power cutters are typically theoretical calculations determined through engineering formulas. Since they are not an actual cutting force measurement, advertised cutting forces may not accurately represent usable forces or what a cutter can do in the real world. There may be more to it than just these numbers.
- Blade thickness is important. In our testing, the cutters that went right through the thickest Boron B-pillars without hesitation all seemed to have specially designed thick blades. The blade thickness held the blades steady and allowed the Boron and the mild steel wrapped around it to be cut completely through.
- Blade shape or design may be another significant factor as well. The Boron testing evaluated different blade designs; radius, elliptical, serrated and a combination radius/serrated unit. There were successes and failures with each style. Many times, the common radial blade design caused the tool to crush the multiple layers of metal into a tight bundle before it was able to try to cut the B-pillar. In some cases where the power of a tool was marginal, the crushing would occur and then the tool would stall out. In cases where serrations in the cutting edges of the blades allowed the pillar or roof rail to start tearing initially as the blades closed, the cutter may make it through the Boron.
- It became apparent during our testing that power cutters are weakest when the blades are fully open and gain strength as the blades close. Their strength is also greatest at the deepest point near the pivot pin. In our real-world testing, this meant that positioning a cutter at a 90-degree angle to a B-pillar may not allow the cutter to cut through the Boron, especially if the blades are short or small in size. By simply turning the tool parallel to the side of the vehicle and getting a different bite, we were able to have the same tool successfully cut through the Boron in some cases. Don't give up if your cutter stalls out. Change your attack angle and go again.
- The newer cutters that were able to cut through the Boron seemed to have larger cylinder bodies. They also were most successful when they severed the metal in one continuous motion, almost a shocking action. Advanced steels stress first, then fracture with a sound similar to that of breaking glass. Due to the larger cylinder body size, it takes more fluid to move the piston and force the blades closed on the new cutters. A problem could occur if a department upgraded to a new-generation cutter, but hooked it up to an older power plant with a small reservoir or a low-flow pump. The cutter would move slowly, take longer to build to maximum pressure and may seem to have poorer performance than the older cutter it is replacing. Operating new cutters through existing hose reels may further diminish the performance of the tool when attacking advanced steels.
- When a cutter was out gunned by the Boron, there was a tendency for the blades to spread apart from each other as the tool stalled out. Rescue personnel should monitor the alignment of the ends of their cutter blades when cutting on late-model vehicles. Any spreading movement of the blades apart from each other is a bad sign — a red flag to stop and reposition.
- One final point is that the advanced steels vary in thickness throughout the structure of any given vehicle. There is no physical indication of whether the steel roof pillar or the area of the B-pillar you are cutting for example is or isn't advanced steel. The best advice if your cutter stalls out during what you expected to be a routine cut is to "reposition, relocate, and retry." Reposition the tool in relation to the piece being cut with a position parallel to the B-pillar being the most likely angle of attack. Relocate a few inches up or down from where you made your initial attempt to maybe get into thinner metal or even hit some mild steel soft spot. Then retry your cut and be patient in allowing your power plant to develop full pressure. Our testing criteria consisted of a hold for 10 seconds and, in some cases, the tool made it through only after a five- to eight-second delay when full pressure finally built up in the system.
RON MOORE, a Firehouse® contributing editor, is a battalion chief and the training officer for the McKinney, TX, Fire Department. He also authors a monthly online article in the Firehouse.com "MembersZone" and serves as the Forum Moderator for the extrication section of the Firehouse.com website. Moore can be contacted directly at [email protected].
THE SERIES...
- Part 1: More Steel
- Part 2: Advanced Steel
- Part 3: Cutting Tools
- Part 4: Power Cutters
- Part 5: New Rescue Techniques
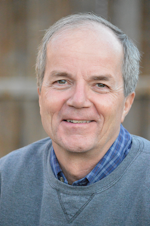
Ron Moore
RON MOORE, who is a Firehouse contributing editor, recently retired as a division chief with the McKinney, TX, Fire Department and now serves with Prosper, TX, Fire Rescue. He self-published the Vehicle Rescue 1-2-3 training manual and serves as the forum moderator for the extrication section of Firehouse.com . Moore can be contacted directly at [email protected].