Tools & Technologies: The Thermal Stability of Your Structural Turnout Ensemble
Thermal stability of structural turnout gear’s component materials is an important factor when selecting new gear. In general, thermal stability describes a material’s ability to remain unchanged when exposed to heat. In relation to firefighting gear, thermal stability is often used to explain changes in the performance of turnout gear after exposure to heat. Materials used in structural turnouts can be compromised by a multitude of thermal conditions – from sudden flashover to extended heat exposure in sub-flashover conditions (i.e., extremely high temperatures for short periods or less extreme temperatures for longer periods). Thermal stability is an important indicator of the durability of the protection provided by your gear.
Structural turnout gear does much more than protect you from extreme heat. Each layer in the ensemble’s composite – the outer shell, thermal liner and moisture barrier – provides different aspects of protection. The outer shell is your first line of defense for many hazards, including protection against cuts, tears, punctures and direct flame. The thermal liner provides the greatest resistance against heat transfer through the garment to your skin.
The moisture barrier serves two roles:
• It keeps the thermal liner dry by blocking liquid penetration from water, blood, body fluids, and the five common chemicals listed in National Fire Protection Association (NFPA) 1971, Standard on Protective Ensembles for Structural Fire. Fighting and Proximity Fire Fighting, 2007 edition.
• It helps reduce heat stress by allowing internal moisture vapor from perspiration to escape from the ensemble.
Because of the specific types of protection these three components offer, they require different materials and constructions. Today’s outer shells and thermal liners are made primarily with fibers that are inherently flame and heat resistant. Moisture barriers, however, are constructed with more than just inherently flame- and heat-resistant fibers. They generally include a polyurethane layer, which tends to be more susceptible to change from thermal exposure. Therefore, the technology used to engineer moisture barriers is very important to their thermal stability. Thermally stable moisture barriers are more likely to maintain their performance properties, especially breathability, after being exposed to heat.
The NFPA 1971 Standard specifies the minimum performance requirements for new turnout gear. Within this standard, certain performance requirements specify pre-conditioning of the test samples as an attempt to address some durability issues. Although you can specify turnout gear with performance requirements that exceed the standard, you may also want to ensure that your gear maintains its performance throughout its useful life. Change in components due to thermal exposure can affect the overall performance or durability of your structural turnout gear. Therefore, when selecting the most appropriate gear for you or your department, it is important to consider the performance of each component before and after heat exposure.
Thermal stability of the outer shell
The outer shell is engineered to provide protection against flames as well as cuts and abrasion from objects you may encounter on the fireground. Today’s NFPA-certified outer shells are made with inherently flame- and heat-resistant fibers, such as Nomex®, Kevlar® and PBI™ fibers. These fibers are spun into yarns and then woven into strong flame- and heat-resistant fabrics. After being exposed to high heat, they still maintain their flame-resistant properties; however, over time, some of these fabrics can become brittle and stiff from heat exposure, which decreases their ability to resist cuts and tears.
Most outer shells will change color when exposed to high heat. A color change in the outer shell can be used as an indicator that the turnout gear has been exposed, which may warrant an examination to determine if it should be repaired or replaced.
Thermal stability of the thermal liner
The primary purpose of the thermal liner is to provide insulation against the heat you encounter on the fireground. Thermal liners are often made with fibers similar to those used in outer shells. Thermal liners typically include a non-woven structure made by entangling and interlocking the fibers. This type of construction gives the material sufficient loft, allowing it to trap a significant amount of air. The amount of trapped air is a key in providing thermal protection – the more air trapped in the liner, the better the thermal protection, with the air acting as an insulator against heat transfer.
Today, the concern with thermal liners is more often the mechanical stability of the non-woven construction than its thermal stability. Heavy wear, abrasion and compression over the life of the turnout gear can reduce the loft of the thermal liner, which affects its performance. Therefore, it is important to choose a high-quality, well-constructed thermal liner. However, when a thermal liner gets wet, its insulating properties can decline significantly. Keeping the thermal liner dry provides more consistent thermal protection, and the moisture barrier plays a key role in keeping the thermal liner dry.
Thermal stability of the moisture barrier
The moisture barrier prevents water and other fireground liquids from entering the gear, keeping the thermal liner and your body protected from these outside elements. In addition, the moisture barrier’s breathability enables perspiration vapor from your body to escape through the ensemble. This is important because it helps your body manage heat stress, and it helps keep the thermal liner dry so it can continue to provide the appropriate thermal insulation. To maintain consistent breathability throughout the life of your gear, moisture barriers should be thermally stable.
Today’s moisture barriers are usually constructed by combining polytetrafluoroethylene (PTFE) membranes, polyurethane layers and inherently flame-resistant textiles. PTFE is an inert, stable material that resists change caused by most types of exposure, including relatively high heat. Polyurethanes, on the other hand, vary in their make-up and can be susceptible to change when exposed to high heat, and some are not stable when exposed to even moderate amounts of heat.
These changes can affect both the breathability and the durability of the moisture barrier. For this reason, it is critical that moisture barriers are engineered to maximize their thermal stability so that these properties do not change over time and/or after use. The specific PTFE and polyurethane materials selected – as well as the technology used to construct the barrier – have a direct impact on the moisture barrier’s thermal stability and its ability to maintain protection and breathability after exposure to heat.
Testing for thermal stability
There are many test methods and specifications that address the performance of new turnout gear; several of these test methods can also be used to evaluate the performance of the individual composite layers after heat exposure. For outer shells, ASTM D5587, Standard Test Method for the Tearing Strength of Fabrics by Trapezoid Procedure, is one method that can be used to compare its strength before and after various types of heat exposure. In this test method, the shell fabric’s strength is determined by measuring the amount of force required to tear the fabric. A decrease in tear strength after heat exposure indicates that the performance of the outer shell has been affected (see Figure 1 on page XXX).
For a thermal liner, one of the major causes of reduced performance is change to its physical structure. Visual inspection is one of the best ways to determine if the thermal liner has been compromised. Any sign of pilling or tearing is an indication that the mechanical stability of the thermal liner has been affected.
The ISO 11092 standard, Textile – Physiological – Measurements of Thermal and Water-Vapour Resistance Under Steady-State Conditions, can be used to evaluate a moisture barrier’s breathable performance both before and after heat exposure. Individual components or the entire ensemble can be tested for water vapor resistance, which is one method to measure breathability. This breathability is determined by measuring the amount of water vapor that can pass through a material in a given amount of time. The more easily the vapor can pass through a material, the more breathable it is. Therefore, a moisture barrier with a low resistance allows the perspiration vapor from your body to escape more easily.
Test results that show an increase in water vapor resistance after heat exposure indicate that the moisture barrier may have been affected by the heat. As shown in Figure 2 (see page XXX), moisture barrier A maintained a consistent level of breathability, with resistance of approximately 5 m2Pa/W before and after exposure. Moisture barrier B, however, became significantly less breathable after heat exposure, with resistance increasing from approximately 8 m2Pa/W before to 17 m2Pa/W after heat exposure.
Durable performance of your gear
When you or your department purchases new turnout gear, it is important to consider the thermal stability of the individual layers (outer shell, thermal liner and moisture barrier). Keep in mind that performance of new gear may differ from its performance after it has been exposed to various levels of heat – especially if the components themselves are less thermally stable.
Breathability after heat exposure directly affects the performance of your moisture barrier, but it can also indirectly affect the performance of your thermal liner. If the moisture barrier is compromised, the thermal liner may not be as dry or it may take longer to dry out. Therefore, the moisture barrier manufacturer’s test data from before and after heat exposure can be a useful tool when selecting the best combination of components for your gear.
It is important to ensure that each component of your turnout gear maintains adequate performance (whether it’s strength, insulation, or breathability) throughout the life of your gear.
PAUL DACEY is a product development engineer with W.L. Gore & Associates Inc. For more than 19 years, Dacey has developed new technologies and products for fire, public safety, and military professionals, with an emphasis on CROSSTECH® moisture barriers. Dacey holds a bachelor of science degree in mechanical engineering and a master of business administration from the University of Delaware. Kevlar® and Nomex® are registered trademarks or trademarks of E. I. du Pont de Nemours and Co. or its affiliates. PBI and design are trademarks of PBI Performance Products. CROSSTECH, GORE and design are trademarks of W.L. Gore & Associates Inc.
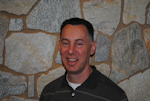
Paul Dacey
PAUL DACEY is a product development engineer with W.L. Gore & Associates Inc. For more than 19 years, Dacey has developed new technologies and products for fire, public safety, and military professionals, with an emphasis on CROSSTECH® moisture barriers. Dacey holds a bachelor of science degree in mechanical engineering and a master of business administration from the University of Delaware. Kevlar® and Nomex® are registered trademarks or trademarks of E. I. du Pont de Nemours and Co. or its affiliates. PBI and design are trademarks of PBI Performance Products. CROSSTECH, GORE and design are trademarks of W.L. Gore & Associates Inc.