Fire apparatus, like most mechanical objects, have life expectancies and at some point during that period there will be a day of reckoning. Is it time to repair and refurbish or send it down the road?
As the economy traveled further down the recent rocky road, many communities were forced to defer scheduled apparatus replacements and perhaps even defer maintenance. They are now at a crossroads, having to make some tough choices about their fleets. In this Apparatus Roundtable, Firehouse® Magazine speaks to a cross-section of apparatus mechanics and maintenance shop managers to get their suggestions and advice on whether it is time for fire departments to repair or replace rigs.
Evaluate honestly
Dave Schreier, president and founder of Emergency Apparatus Maintenance Inc. in Lino Lakes, MN, says the question boils down to an honest evaluation of the chassis. If the foundation is not solid, there is no point in putting more money into a vehicle that should be shipped out to pasture, he says.
“The biggest mistake the departments make is they skip the basics,” Schreier says. “They need professionals to look the whole truck over and make an assessment.”
He says too often, fire departments fail to look at the frame and the subframe for corrosion or damage. Frame problems can scuttle any plans to refurbish or repair apparatus, making the price prohibitively expensive and not worth the effort, Schreier says.
“It all goes down to the foundation and that’s the part that’s most often overlooked,” Schreier says.
Departments also must analyze the major components of the apparatus, like the hydraulic systems of an aerial, the health of the engine and transmission and the capacity of the pump, Schreier says.
“Do an oil sample, test the pump and look at the electrical load,” he says. “An NPFA (National Fire Protection Association) pump test will go a long way to determining the overall condition of an apparatus. …What you’re looking for is the apparatus ready and worthy for a refurbish – is it basically sound?”
Emergency Apparatus Maintenance Inc. was founded in 1987 by Schreier, who is a professional truck mechanic and a retired volunteer fire chief with 25 years of service. His business provides services to more than 2,500 fire and emergency medical departments in the Midwest, from Minnesota and Wisconsin to Colorado and parts of Wyoming and Montana south to Oklahoma and Arkansas. The company also maintains a fleet of 17 fully stocked mobile service trucks and 12 mobile pump-testing units.
Assess “big-ticket” items
Steve Towers, the founder and owner of Fire Service Repair in Snohomish, WA, also believes fire departments mulling replacement or repair must look at the “big-ticket” items before making any serious decisions. Those big-ticket items include the pump, engine and transmission, Towers says.
“An NFPA 1911 pump test is like a stress test on a fire truck,” Towers says, referring to the NFPA’s Standard for the Inspection, Maintenance, Testing and Retirement of In-Service Automotive Fire Apparatus. “If you have problems with your truck, it will show up.”
Towers, who has worked in the mechanical repair field for more than 43 years, and 19 of those as in professional emergency vehicle repair, says if more than one of those major components show serious deficiencies, the fire department must make a decision on whether it wants to spend lots of money just to get the vehicle back up to a condition where it could be refurbished. Engines and pumps can cost upwards of $25,000 each to replace, Towers says, noting that if they both need to be replaced, it seriously undermines the prospect of saving the apparatus.
“That’s going to kill that truck from being refurbished,” he says.
Towers says fire department should also consider the quality of the truck to begin with. If it is way out of NFPA compliance, with an open cab for instance, or was built on a low-quality cab and chassis with not much seating, departments probably ought not to spend big money on saving it.
Rust and corrosion is also a consideration, Towers says, although it is not a huge problem in his area, but occasionally, he will see an apparatus in his shop that is from “back East” that has rust problems. Corrosion problems can be fatal for apparatus, he points out.
If all the “big items” check out, Towers says it is time to start looking at optional equipment and accessories. If a lot of those systems are in disrepair, that may signal the end of the road for a truck too. “All of those things can add up,” Towers says.
Abiding by city policy
Floyd Schiller is the head of Denver Fire Department’s fleet division with the title of assistant master mechanic. He has been head of the division for 10 years and a mechanic for 19. In his job, he is responsible for maintaining the apparatus in the city’s 30 fire stations that collectively run about 100,000 calls annually. That means each of his trucks run about 3,000 to 4,000 calls per year.
Repair or replace is not an obvious option for Schiller. By city policy, apparatus are replaced every 20 years. “When we retire apparatus, it’s pretty beat up,” Schiller says.
Schiller says that at least once during an apparatus in service time it receives an engine rebuild and spends 14 years in front-line duty.
“When a new engine can cost $400,000 or more, it’s easy to make sense of a decision to put $20,000 to $30,000 into one to keep it going,” Schiller says.
Keeping high-use apparatus reliably on the road requires constant maintenance Schiller says. That’s why each Denver apparatus receives what he calls an “annual,” where everything on the rig, “from bumper to bumper, top to bottom” is checked, repaired and maintained or replaced as needed.
Colorado does not require annual Department of Transportation (DOT) safety inspections on fire apparatus, as some states do, but Schiller says conducts them anyway to make sure the city’s investment in the equipment is maintained.
There are times when it just does not make sense to spend money on worn-out apparatus at the end of its life cycle, Schiller says, noting that for him, a $125,000 repair bill on a 19-year-old rig is not cost-effective as it will soon be retired. That circumstance and any kind of collision or accident may take an apparatus out of service quicker than its 20-year expected life cycle.
Schiller says he takes pride in his shop and his people as they are expected to be masters in many facets of apparatus repair and can machine and manufacture obsolete parts that may be unavailable. That helps keeps the Denver rigs on the road longer, whereas other departments may have to think about retiring apparatus because of unavailable parts.
Schiller says that in many cases, replacing an apparatus can come down to a decision about “comforts and operator conveniences” over performance issues.
Apparatus today doesn’t significantly pump or haul water or operate differently than its kindred of 30 years past.
“I actually like older apparatus and keeping them on the road,” Schiller says. He comments that there are many safety features built into new apparatus that departments should consider when making a decision to repair or replace.
Weighing options
Douglas “Smokey” Horton is the service manager for Jerome Fire Equipment Co. in Clay, NY. As a former fire chief with the Mexico, NY, Fire Department and with 28 years in the business as an emergency vehicle technician and 13 years as the repair company’s service manager, Horton has some clear thoughts about whether to repair or replace.
“If you’ve got a low-dollar, cookie-cutter truck on a commercial cab and chassis with a 1,000-gpm pump and a 1,000-gallon tank, it makes no sense to put $100,000 into it,” Horton says. However, he adds, an apparatus with a custom cab with a stainless-steel body built in the late 1990s is prime for repair and refurbishing.
Apparatus with lots of options, like generators and light towers and add-ons, also rank higher when considering repair and refurbishing or replacing. Along with many of his colleagues, Horton believes a thorough evaluation of the apparatus is prerequisite to any decision-making.
“You need to have someone get on a creeper and look the entire truck over, looking for oil leaks, problems with the frame, the suspension, everything,” Horton says. There are many little factors like door latches on the cabs that may need repair or windshields that may be fogging at the edges, which is a sign they are de-laminating.
Even tires must be considered, Horton says. New York State’s DOT says tires are to be replaced every seven years, but Horton says depending on the condition, they may last a little longer, perhaps 10 years, but they should never be left on 20 years or longer.
“That’s just too old,” he says. “They’re hard and they’re not the same they were 20 years ago.” He said there have been some significant crashes attributed to tire failure on apparatus over the years.
A well-maintained apparatus with a good written service history is always a better bet for repairs and refurbishing, Horton says. Of course, there are always the economics to consider when deciding whether to repair or replace. “There’s only so much money in any community’s budget,” Horton says.
And Towers, the owner of the repair facility in Snohomish, Washington state, agrees. As a former career firefighter and a fire commissioner for Snohomish Fire District 4, Towers says he learned a way to help take the financial sting out of the decision of whether to repair or replace.
“The answer is an equipment replacement fund,” Towers says. “You need to put aside money to buy new apparatus when it’s time…It needs to be untouchable.”
Schreier, of Emergency Apparatus Maintenance in Minnesota, says communities also need to figure out what kind of repair or refurbishing they want to do. Some departments are OK with a fresh coat of paint and some new lights for an inexpensive remedy, while others want something more substantial with a bigger price tag, Schreier says.
“You have to think about the value to the community,” Schreier says. “You have to look at the goals of the department and its mission.”
Schreier says that recently, he has seen a leveling off of substantial repairs and refurbishing in favor of replacement and buying new and takes it as a sign the economy may be improving. But for those communities and departments that are still feeling the pinch, Schreier says, repair and refurbishing is a good way to get by for a little longer.
“Refurbishing is a way to push off that purchase for eight or 10 years and help save some money,” Schreier says. “But, it all goes back to the foundation. You have got to take a look at what issue the truck might have and then make a decision.”
ED BALLAM, a Firehouse® associate editor, is a captain with the Haverhill Corner, NH, Fire Department and a nationally registered EMT. He is also a deputy forest fire warden for the New Hampshire Division of Forests and Lands. He holds certifications in emergency vehicle operations and pump operations.
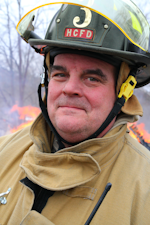
Ed Ballam
Ed Ballam served as associate editor for Firehouse. He is the assistant chief of the Haverhill Corner, N.H. Fire Department, and a National Registered EMT. He is also a Deputy Forest Fire Warden for the New Hampshire Division of Forests and Lands. Professionally, he's been a journalist for over 35 years working for a variety of publications, including employment as managing editor of a national fire service trade journal for more than a decade.