SUBJECT: Advanced Steels: Part 8
TOPIC: “Pie Cut” Work-around Technique
OBJECTIVE: Given a scenario where an occupant is trapped and the B-pillar needs to be moved or removed, the rescue team will become familiar with alternate techniques to accomplish B-pillar tasks.
TASK: The rescue team shall practice and become proficient in accomplishing a “pie cut” work-around technique
In the November 2013 University of Extrication column, we looked at the various shapes and designs that auto manufacturers are using for advanced steels inside the structure of their vehicles. It was mentioned that a very difficult design to cut through is frequently a pipe-shaped design inside the hollow of a pillar.
In this article, we will take a closer look at an advanced steel pipe that is installed inside the hollow of a B-pillar on a late-model SUV. This closer look will also explain why a “pie cut” work-around technique might just work when rescuers encounter difficulty cutting into or across what is an otherwise normal-looking B-pillar.
The particular B-pillar design incorporates the familiar curved, C-shaped ultra-high-strength steel as one inner layer of advanced steel inside the B-pillar. What is important to note, however, is that in addition to this one layer of hot-stamped Boron, there is also a hollow Boron pipe within a portion of the pillar. As interesting as this pipe is, it must be noted that the pipe does not extend the entire length of the pillar. Instead, the pipe occupies only an upper, “impact zone” area inside the hollow of the pillar.
One of these pillars was removed from the late-model SUV as part of a research project on vehicle construction. After removal, the pillar was split open to reveal the inner Boron pipe section inside. As you can see, the hollow pipe is of a small diameter but has relatively thick walls. The opened pillar was then placed next to an intact pillar to orient the viewer to where the pipe would be inside an actual pillar.
Closer review showed that the pipe is welded into position with its lower end just above the top door hinge area. The tip of the Boron pipe extends to almost the top of the pillar.
At a crash scene where this structural design is encountered, rescuers would not be able to see the inner Boron pipe. Instead, if the pillar were required to be removed for extrication purposes, the crew would most likely attempt to make a horizontal cut across the pillar near the roofline. If the cutter is just a few inches below the edge of the roof, it might not only be trying to cut the structure of the pillar but might also be attempting to cut into the reinforcement pipe as well.
Even with a new generation power hydraulic cutter, this boron steel pipe shape has proven to be very difficult to get through. Several brand new cutters, designed to cut through advanced steels such as Boron, have failed to make this cut. This author has seen new rescue cutters stall out or even break a blade during this effort.
If a responder is trained to recognize that advanced steels in the structure of vehicles is a reality, then having a tool stall out while making a cut across the pillar should prompt the rescuer to try a work-around technique to complete their task.
In this particular case, with this particular reinforced B-pillar design, the alternate “pie cut” work-around technique might lead to success. This is not a new skill; it is from years past and has until recently not been a popular technique. To accomplish it, two diagonal cuts are made into the roofline structure, one from each side, to separate the top of the B-pillar from the roofline. If this effort succeeds, the cuts are into the softer metal, the pillar is detached, and can then be moved or removed to free the trapped occupant.
TASK: The rescue team shall practice and become proficient in accomplishing a “pie cut” work-around technique
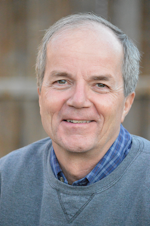
Ron Moore
RON MOORE, who is a Firehouse contributing editor, recently retired as a division chief with the McKinney, TX, Fire Department and now serves with Prosper, TX, Fire Rescue. He self-published the Vehicle Rescue 1-2-3 training manual and serves as the forum moderator for the extrication section of Firehouse.com . Moore can be contacted directly at [email protected].