Vertical Ventilation of Strip Mall Fires
Vertically ventilating the roof of a strip mall can be categorized as a low-frequency/high-risk event. Less than 10 percent of all fires are located in stores or strip malls, but when these fires do occur, there are several risk factors, including common attics, large open spaces with increased fire loads, and engineered trusses, to name a few. Considering that many firefighters do not have real-life experience with these structures, it is important to review the skills involved to ensure that truck companies are prepared to safely and confidently go to the roof and vent.
There has much discussion in the fire service about coordinating vertical ventilation with fire suppression and the effects of entraining air. With respect to that fact, I believe there is still a place to support interior operations and the fireground strategy with vertical smoke removal. Key to this is for both the company officer and incident commander (IC) to know the type of building and truss system they are dealing with to help support the incident action plan (IAP) and current fireground strategy. Here we will walk through the process of an effective operation to ventilate a strip mall fire.
Strip malls
Strip malls form a retail complex typically in a long building consisting of various types of occupancies located in adjacent spaces. They are separated by partition walls, and some are anchored by a big box retail store like Kohl’s or Target.
Strip malls were first developed in the 1950s as a convenient way to attract customers to local shops. Some have since become derelict, while some are making a resurgence. Whether strip malls thrive depends on several factors, such as if they are located in a high-density area with strong employment and can conveniently offer products to compete with online options. Most fire departments in the urban setting have strip malls in their community, and the chances are good of having one of the over 100,000 strip malls or similar stores in the United States located in your first due.
Strip mall exterior construction includes tilt slab, block or wood, and the truss systems can be engineered trusses, metal or combinations built in a panelized or parallel chord configuration. Common widths on these businesses range from 20 to 30 feet wide and have depths of 60 to 75 feet, with dropped ceilings of about 10 feet below a common attic. The typical front, or A side, is primarily composed of glass in the form of large windows and doors. The rear of most strip malls includes outward opening steel doors and roll-up doors, and some have loading docks.
An inherent danger in the layout of strip malls is the open floor plan, which contain an abundant amount of products that have a very wide range of hazards. These modern materials burn fast, increasing the heat release rate (HRR), which may cause the fire to extend upward into the common attic, where it can quickly spread horizontally and make the roof unstable for the ladder company to perform its tasks.
Preplanning
One of the best steps for any ladder company is to preplan the strip malls in their first due. Preplans should include identifying the types of businesses as well as the roof support system, including the direction of the trusses and access to the rear. Knowing the height of the parapet may indicate the need for an attic ladder to step off onto the roof from a bucket or aerial ladder. Remember, the scupper holes (openings in the wall that allow water to drain off the roof) indicate the distance between the roof height and the top of the parapet wall, and they are usually located in the rear or sides of the structure. There are not many “always” in life, but the ladder crew must know the direction and type of trusses (parallel chord or panelized) if they are to safely navigate the pathway to the vent location and stand safely on supporting trusses to perform the cut sequences correctly. A good preplan should also indicate if there are any fire walls and, if so, their location.
Spotting
Before accessing the roof, the captain must select a strategic position to park the truck based on function, strategy and potential fire spread. Repositioning the truck is dysfunctional at best, and once a fireground gets crowded, it is sometimes nearly impossible to relocate. Spotting on a corner offers a good scrub area and protection from a building collapse.
Further, park the apparatus to maximize your aerial reach, for example, backing in if you have a rear-mount turntable. Oftentimes, the C/D or B/C corners in the rear offer a place to avoid the congestion that develops in the front of the occupancies. A good preplan will confirm access to the rear and alert you of hazards, such as powerlines or narrow driveways.
Park on the unburned side of the building, being aware of current fire conditions and location. One additional note is to preplan the immediate area where your outriggers will be deployed so there will be enough room to extend them without hitting a curb or another obstacle.
Once the order is received to vertically ventilate, the captain must decide how they will access the roof, either by use of the aerial (and bucket) or by a ground ladder. Factors that may influence this decision are department standard operating procedures (SOPs), how many members can fit in the bucket with all their equipment, and the time it takes to set up the outriggers and load members into the bucket versus throwing a ground ladder.
Crew assignments
Crewmembers must know their assignments prior to “making” the roof, whether they will be the sawyer or punch person, as well as what equipment they need to take to the roof. A common example of tools needed: two saws, trash hook(s), a flat-head axe or two, radios, flashlights and a thermal imaging camera (TIC).
Crews must have practiced the “dance” or cut sequence that they will be performing, which will be dependent on the type and direction of the trusses—whether they will be cutting from a purlin or glu-lam or with or against parallel chord trusses. This is not the time for discussion or instruction from the captain or “practice time.” This is where cutting on ventilation props will pay its dues.
Roof operations
Once on the roof, an inspection hole cut out of the way of travel is a must. As mentioned earlier, this process determines the truss type as well as decking material, its depth and if there is insulation below the decking.
To accomplish this, start with a 45-degree angle cut away from the parapet wall, as this will ensure that you “roll” over a rafter (or two) and continue to make cuts to form a triangle-shaped hole that is big enough to feel underneath or stick your head in to visualize trusses. It is imperative that the person determining the trusses communicate with the crew the type and direction of trusses. The use of hand signals is helpful, as the saws make hearing conditions tough.
Next, walk on the ledger wall toward the desired vent location while making small smoke indicator holes in the roof at appropriate intervals (approximately 20 feet apart at first and closer together as you get nearer to the fire). The holes should be no larger than the width of the saw blade and in the shape of a triangle. This will allow any smoke to “push” through the hole as an indicator of conditions below.
Be sure to remove any insulation underneath the roof deck that might prohibit the exit of smoke, and take a TIC reading to make comparative temperature readings as you get closer to the seat of the fire.
As you move closer to the fire, the smoke will probably become darker, and when it holds its triangular shape for about 12 to 18 inches above the roofline, there is enough heat/fire causing pressure for you to consider the “event” is underneath you or at best close enough. It is important at this point to consider the time needed to cut the vent hole versus your present location, and maybe consider backing up a little bit so crewmembers are not directly over the fire when they finish operations.
If you need to move toward the center of the roof to make your ventilation cuts, make sure to locate a support member to walk on by “sounding” the roof or making another small inspection hole. The size of the ventilation hole will be indicated by the area sounded with the trash hook by the captain, and the first cut or “head cut” will determine the length of the vent hole. Again, rehearsing on the ventilation prop will help with foot placement, cut sequences and whether to use one or two sawyers.
The captain should continually keep their head on a swivel to any changing conditions on the roof and should indicate when they want the louvers opened up. Be aware of wind conditions that might blow smoke into the vision of operating sawyers.
Once the hole is complete, the captain should exit the same way, if safe, by sounding the roof and using the smoke indicator holes as a sort of “bread crumb” trail. Next, they should give a roof report to command when in a safe place to do so. A good roof report will contain confirmation of vent hole, product emitting from the hole, any fire involvement in the attic, roof type and load, roof integrity and a personnel accountability report (PAR). A confirmation of when the crew is off the roof and back on the ground should also be given with a notification of the need to recycle or availability for next assignment.
Final thoughts
Each department has its own set of SOPs to follow when it comes to vertical ventilation, and depending on what part of the country you live in and the culture of your area, objectives and styles may differ from the suggestions of this article. But having a plan for your crew ahead of time and all members on the same page should be a goal of every company going to the roof.
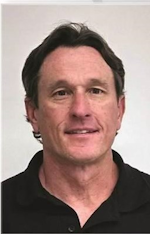
Gibby Gorman
Gibby Gorman recently retired from his fire service career after nearly 33 years, which began in 1986 with the Tempe, AZ, Fire and Medical Department, where he served for 27 years. During that time, Gorman: worked as a downtown ladder captain for 14 years; responded on the SCUBA Rescue Team; worked on the hazmat team; served as coordinator for the Regional Technical Rescue Teams; taught fire science classes at the community college level; and presented ladder tactics for Firehouse World conferences,, including in 2020. In 2013, he became a battalion chief for the Maricopa, AZ, Fire and Medical Department. Gorman created Southwest Firefighting Concepts. He received his bachelor’s degree from Arizona State University.