Topic: Comparison of Steel Tensile Strengths
Objective: The rescue team will better understand advanced steel tensile strength ratings and how they relate to that of mild or high-strength steel.
Task: Within the rescue team’s organization, members shall develop a means of relating the relative tensile strength of mild and high-strength steel to the tensile strength of advanced steel.
Rescue personnel at extrication incidents work with their tools as they deal with jammed, crushed, bent or otherwise damaged structural components of a vehicle, especially doors. The most common material that confronts rescuers is steel: primarily mild, high-strength or ultra high-strength steel (UHSS).
Boron, representing the class of UHSS, commonly referred to as advanced steels, is now a common term that rescuers have become familiar with. Boron, however, is a trade name for only one type of UHSS. There are others in this category such as transformation induced plasticity steel (TRIP), dual phase (DP) and martensite steel.
The measure of the “strength” of automotive steel is its tensile strength—the force required to stretch it as it is pulled apart. This force is measured in units called megapascals (MPa) and is given a number. The higher the number, the stronger or tougher the steel.Mild steel is generally between 275 to 350 MPa with high-strength steels having megapascal ratings up to slightly over 700. Today’s ultra high strength steels, such as the familiar Boron, have megapascal ratings up to 1,500 or more.
So how do rescuers relate this technical and scientific engineering information about steel to our real-world challenges at a vehicle crash?
A simple and effective training technique to better understand the megapascal ratings of steels and to be able to compare and remember mild steel strength compared to the strength of advanced steel is to use common U.S. coins, including the penny and the nickel.A U.S. penny is 1.55 mm thick while a nickel is 1.95 mm thick. To show the relative strength of modern steel, use a reciprocating saw and make two clean cuts across the A- or B-pillar of a vehicle so a section can be removed.
Take a penny and show that a layer of steel inside a cross-section of the pillar you just cut is as thick as your penny. Then stack seven more coins on top of your penny. This eight-penny-thick stack represents what your rescue tool is confronted with if it were ultra high-strength steel, such as Boron, present inside that pillar you just cut.The penny comparison is just a visual training tool that will provide at least some sort of understanding that what we see is not what our rescue cutter tool “sees” and has to deal with. The difference in thickness between a penny and a nickel might seem trivial but it can be huge to your cutter. Try the 8-1 stack of each and see for yourself.
The Penny Test
- Grab a reciprocating saw
- Make two clean cuts across the A- or B-pillar of the vehicle
- Remove the pillar
- Compare the width of the steel with a penny
- Stack eight pennies together and this represents UHSS
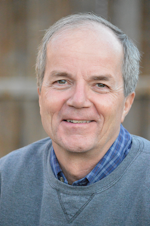
Ron Moore
RON MOORE, who is a Firehouse contributing editor, recently retired as a division chief with the McKinney, TX, Fire Department and now serves with Prosper, TX, Fire Rescue. He self-published the Vehicle Rescue 1-2-3 training manual and serves as the forum moderator for the extrication section of Firehouse.com . Moore can be contacted directly at [email protected].