University of Extrication: Aluminum Vehicle Structures
Topic: Aluminum alloy in Ford F-Series pickups
Objective: Familiarization with aluminum alloy during extrication work
Task: The rescue team shall develop techniques for completing vehicle-rescue tasks when confronted with aluminum alloy structural components
Ford Motor Company initiated the use of military-grade aluminum alloy for significant portions of the structure of its F-Series pickups beginning with the 2015 F-150. Since that time, the aluminum alloy has been incorporated into the structural components of other F-Series models, up to and including the F-550. (The pickup chassis and several other components continue to be composed of steel on those vehicles.)
What’s promoted as military-grade aluminum alloy is a version of what’s known within the industry as 7075 aluminum; it’s a metal that features a tensile strength of 83,000 psi.
Vehicle-rescue personnel must be aware that aluminum alloy exists in the structural areas of F-Series cabs and bodies, know where it is and isn’t located and be able to complete vehicle-rescue tasks while dealing with steel or aluminum alloy.
Use of aluminum alloy isn’t new to the automobile industry. Luxury vehicles, such as some of those that are made by Audi, Jaguar, Porsche, Range Rover and Tesla, have aluminum body panels. Audi has used aluminum for the structure of its flagship A8 sedan for many years.
Aluminum can be formed into automotive structural members or a flat metal panel for use in hoods, door panels, fenders and trunk lids.
What difference does it make when a rescue task must be accomplished and the team encounters, say, an aluminum roof pillar? Do you do anything differently? How can rescuers best prepare for this material? What tools and techniques work?Picking apart pickups
Research work that involved the cutting up and systematic dissection of several 2015 F-Series pickups produced revealing cross sections of the structure of these vehicles. These cross sections disclosed much about how Ford designs and assembles these popular vehicles.
Rescue personnel first must realize that 7075 aluminum isn’t used for any of the F-Series door hinges, door locks or door latches, although the structure of the door itself is aluminum. So, when confronted by a jammed-door situation at a crash scene, the door lock and latch assembly must be pried, forced or cut through as is done for almost all other vehicles. Patience is required, though, because, when forcing a jammed aluminum door, the material that makes up the door can have a tendency to tear easily. Torn aluminum can create sharp and jagged exposed edges. This makes proper protective clothing that much more important.
By the same token, it’s just as important for rescuers to realize that, essentially, the entire body of F-Series pickups consists of military-grade aluminum alloy: fenders, tailgate, roof pillars, roof rails, rocker channels, floorpan and roof panel.Aluminum flat panels that are found on F-Series doors, hoods and roofs should be considered “soft.” They can be chopped through with an axe or cut open with an air chisel or reciprocating saw quite easily.
Furthermore, the research work found that, essentially, all rescue tools are capable of cutting through a roof pillar, a portion of a rocker channel or any part of the roof rail. (These tools include an air chisel and a flat chisel bit, a reciprocating saw and a metal-cutting blade, a hacksaw and a hydraulic power cutter.) Unlike ultrahigh-strength steel pillars, aluminum alloy pillars yield quickly to these cutting tools.
During the research, a pair of 2015 F-Series cabs were cut up completely by using only two reciprocating saw blades. To be most successful, it was beneficial for the variable-speed reciprocating saw to be run at a slower blade-speed setting. This slower speed setting minimized overheating of the blade and melting of the aluminum while the saw blade made the cut. With a variable setting of 1 (slowest) to 5 (fastest), the third or fourth setting was found to be most effective. Although operating the saw at a high stroke-per-minute speed might seem the proper thing to do, cutting at that speed actually can result in less efficient cutting, greater difficulty operating the saw and more time to accomplish the overall task.A discovery that wasn’t expected was that, in addition to aluminum alloy construction in roof pillars, plastic or foam filler materials were encountered (as well as inside of other structural components). These filler materials are inside of the hollow areas of the pillars at specific points. The plastic foam inserts didn’t slow down or interfere with the use of the power cutter or the reciprocating saw. When the reciprocating saw encountered one of these inserts, there was a slight smell of burning and a few wisps of smoke.
Overall during this research, the aluminum alloy didn’t interfere significantly with or hinder standard vehicle-rescue tasks on F-Series vehicles.No foiling rescuers
Vehicle-rescuers have the ability to accomplish just about anything on F-Series pickups. With an awareness of the presence of aluminum, everything from forcing jammed doors to cutting a vehicle apart to free a trapped occupant can be accomplished with almost any rescue tools using standard and what would be considered otherwise normal vehicle-rescue techniques.
When forcing an aluminum door, be patient. Pry a little, close down, move in and pry a little again.
Extrication from a Potentially Aluminum-Laden Vehicle
- Determine presence of aluminum
- Body panels?
- Door hinges, lock/latch assembly?
- Structure of vehicle?
- Variable-speed reciprocating saw at slower speed
- Anticipate structural filler materials
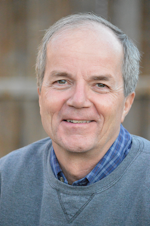
Ron Moore
RON MOORE, who is a Firehouse contributing editor, recently retired as a division chief with the McKinney, TX, Fire Department and now serves with Prosper, TX, Fire Rescue. He self-published the Vehicle Rescue 1-2-3 training manual and serves as the forum moderator for the extrication section of Firehouse.com . Moore can be contacted directly at [email protected].