University of Extrication: Service, Care and Maintenance of Rescue Chain
Topic: Service, care and maintenance of rescue chain
Objective: The rescue team shall create an SOP or protocol for ensuring that all rescue chain is ready for service
Task: Implement a service, care and maintenance program (SCAM) for rescue chain
The purpose of this column is to provide a framework for creating a written document in the style of a standard operating procedure (SOP) that requires servicing, care and maintenance of rescue tools after each use, on a minimum monthly basis and after each real-world incident. The six-step program that’s recommended here can be customized easily and applied to all rescue tools and equipment. After explaining the program, we will use rescue chain as an example.
Although this new program uses a slightly different title, it’s based on selected elements of the newly published NFPA 1937: Standard for the Selection, Care, and Maintenance of Rescue Tools.
Similar to how a successful operation at a fire can depend on well-maintained and properly functioning lengths of hose, rescuers must be assured that all of their rescue tools will perform satisfactorily under the loads and applications to which they are subjected during an incident. NFPA 1937 encourages agencies to create a formal written program that begins with acquiring rescue tools (Selection) and continues through the life of the rescue tools (Care and Maintenance).
Similar to how rescuers already inspect, maintain and document use of rescue rope, a department’s service, care and maintenance protocol, or SCAM program, includes an inventory and checklist for responders to use as they clean, inspect, maintain and document use of the agency’s rescue tools and equipment.
A functioning SCAM program quickly identifies damaged tools that require minor repair before those tools are thrown in with all of the other tools back on the rescue vehicle. Tools that are out of adjustment, broken, in an unsafe, deteriorated condition or otherwise unfit for service either will be repaired or retired from service and disposed of. A “Red-Tag” procedure also is established for when the remedy to a broken or damaged tool or component is beyond the ability of department members through allowable repair work.
Four ground rules, shall we say, for implementing a SCAM program include:
- Personnel who conduct any tool and equipment check shall be provided with and shall wear safety apparel, including eye protection, as determined appropriate by the department.
- If the SCAM program work requires additional repair tools or a dedicated work area, a space within the rescue station building that’s clean and clear of obstructions and hazards is to be made available for use.
- SCAM program work isn’t to be performed beyond the limits of the training and abilities of department personnel. A specific member may be identified as the department’s technician and may be trained, qualified and authorized to make repairs. However, this work shall not exceed what is allowed by the tool manufacturer, using proper replacement parts as specified by the manufacturer.
- After any needed repairs, an operational check and written documentation must be completed before the serviced item is placed back into service.
A written SCAM program that addresses competencies of the NFPA standard could be created for each general category of tool that the department owns: power rescue tools, lift bags, struts, chains, winches, hand tools, etc. The basic steps to completing SCAM program work for each tool category is the same and has a natural flow to it. Remember, a formal service, care and maintenance policy is just one component of the overall program that’s described in NFPA 1937.
Inventory and accountability
Step 1 of the University of Extrication SCAM program begins with gathering all tools and components of the given category and conducting an inventory and accountability check of them.
Members are given the SCAM program sheets for the category. Determine that all agency-owned rescue tools and equipment in the category are present and accounted for. This requires compiling a checklist of all items that are in the department’s rescue inventory by their category.
Cleaning and disinfecting
Step 2 of the SCAM program is cleaning and disinfecting. SCAM program instructions advise members to wipe down tools and components with a clean, lint-free cloth to remove exterior dirt, grease and grime and to repeat the process until the cloth stays mostly clean.
Step 3 calls for rescue personnel to closely inspect each item for signs of physical damage, such as cracks, fluid leaks, nicks, cuts, burrs, stretching, bending and heat or cold damage. Following the inspection, an operational “fit-to-function” check is performed. All accessories and components are connected as the tool is put back together as if it were to be used for a rescue task. Once the tool is reassembled, it’s worked with/operated to ensure that everything functions properly.
Tool readiness
Returning tools and components to in-service status is Step 4. The rescue tool typically is put in its carrying case and placed in the appropriate tray, drawer or compartment on the rescue vehicle.
Minor repairs and adjustments
If a minor glitch or other type of anomaly is discovered during the operational check or the physical inspection and it is something that can be fixed immediately in the field, crewmembers make the repairs (a screw is tightened, a coupling is adjusted, fluids are brought to the proper level) and return the item to in-service status (Step 5). Work that’s determined to be beyond normal field-level tasks may be accomplished by a designated person within the department or a repair “technician” who is trained and authorized by the tool manufacturer to complete advanced repair work.
When the rescue tool or component accessory is found to be or suspected of being damaged beyond the capability of the department’s field-level maintenance, the SCAM program directs that the tool be “red-tagged” as being out-of-service (Step 6). Having a red tag physically secured to the questionable rescue item allows the item to remain segregated from other functional equipment. All of the items that are red-tagged are to be reported as such to a department officer.
Rescue chain
To ensure this SCAM program seems reasonable and realistic, let’s use rescue chain as an example. With that, the assumption is that an agency owns lengths of 3/8-inch rescue chain, which is “certified” as Grade 8. The rescue chain has a working load limit of 7,100 lbs. and a 5:1 safety ratio.
The scenario: A training session in which rescue chain and other tools were used just concluded. In this scenario, the agency has a complete inventory of all of its rescue chain lengths. Therefore, the first step of the SCAM program can be started. All rescue chain, hooks, chain clusters and load binder tools are gathered by the members of the rescue crew and accounted for by them through the use of the rescue chain inventory checklist.
Step 2 calls for cleaning the chain, which means wiping down each length with a clean cloth. This work would remove all of the exterior dirt, grease and grime, so each link of the chain can be seen clearly. A visual and physical inspection of each chain, link-by-link, follows.
After passing all aspects of the field inspection, the chain is determined to be fit to be placed back into service (Step 3).
Step 4 (tool readiness and proper storage) places the chain back where it belongs, typically in a drawer inside of a compartment or hung on a hook in a compartment on the rescue vehicle.
If necessary, minor field repairs and/or adjustments are made (Step 5). With a rescue chain, for example, repairs that are possible can include replacing a cotter pin in a master link at a hook.
For the purposes of this University of Extrication column, let’s say that deformed links, which indicate that the chain was overloaded or exposed to a sharp corner, were discovered. Step 6 would place this chain out-of-service immediately. It would be physically red-tagged and removed from inventory right then and there.
Safe and Reliable
NFPA’s new 1937 standard provides many more details in regard to developing a compliant and safety-oriented written program for selecting, caring for and maintaining rescue tools and components. Creating and implementing this type of rescue tool SOP along with documentation of use and maintenance of rescue tools absolutely must be given consideration by agencies in this era of civil litigation. Complying with NFPA 1937 and creating a SCAM program for all rescue tools and components go a long way to ensuring that everything is in a safe, reliable working condition before used to save lives.
Ron Moore will present “Vehicle Rescue 2021 Update” and “Electric and Autonomous Vehicles” at Firehouse Expo. To register, visit firehouseexpo.com.
SCAM Program
- Tool Inventory & Accountability
- Cleaning & Disinfecting
- Inspection & “Fit-to-Function” Check
- Tool Readiness &
- Proper Storage
- Minor Field Repairs
- & Adjustments
- Out-of-Service & “Red-Tag”
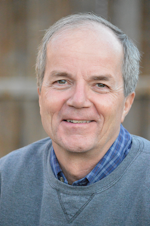
Ron Moore
RON MOORE, who is a Firehouse contributing editor, recently retired as a division chief with the McKinney, TX, Fire Department and now serves with Prosper, TX, Fire Rescue. He self-published the Vehicle Rescue 1-2-3 training manual and serves as the forum moderator for the extrication section of Firehouse.com . Moore can be contacted directly at [email protected].