The Apparatus Architect: Fleet Alternatives to Buying New
Any fire department that recently received bids for a new apparatus recognized that the marketplace has changed, resulting in extended delivery times and a dramatic increase in cost. Macroeconomic conditions along with geopolitical issues created a series of conditions by which the fire apparatus industry is experiencing unprecedented production backlogs, exponential increases in costs for raw materials and electronic components, and labor shortages.
Budgets for capital projects often are determined six months or more ahead of the beginning of a fiscal year, with the anticipation of bidding new vehicles shortly thereafter. In many cases, fleet managers are struggling to acquire needed vehicles because of the increased cost and delayed deliveries (18–24 months). Therefore, apparatus that were slated to be removed from the fleet or to be placed into reserve status now are being relied on to provide frontline service for extended periods. All of these circumstances result in increased operating expenses for and frustrations in stabilizing the vehicle fleet.
Although some departments have sufficient financial resources to afford new apparatus today, others that aren’t funded by the municipal tax base and that rely on fundraisers and donations are at a significant disadvantage. The cost of a new apparatus is beyond the means of many communities.
Several alternatives to purchasing a new apparatus should be considered when evaluating your department’s vehicle fleet, including acquiring a used piece of apparatus and rebuilding one or more current rigs to extend their life cycle.Used apparatus marketplace
Some departments never have been able to afford a new apparatus, and given today’s cost of the latest engine and ladder apparatus, even well-funded organizations that purchased new in the past might find that path beyond their reach. Thus, acquiring a used apparatus that’s newer and in better condition than the one that’s planned to be replaced might be worthy of consideration.
The used fire apparatus market has been relatively stable price-wise over the years, with a slight increase during the period of 2007–2010 because of a combination of the economy, Environmental Protection Agency regulations on diesel engine emissions and changes to NFPA 1901: Standard for Automotive Fire Apparatus.
Furthermore, prior to the pandemic, the availability of used fire apparatus and the subsequent sales of these vehicles didn’t experience year-to-year fluctuations.
Unfortunately, the extended delivery times for new apparatus has affected the availability of high-quality used rigs (a decrease of as much as 40 percent) and the cost of these vehicles (at an all-time high).
Several websites provide resources where potential buyers can input criteria for a vehicle (commercial or custom chassis) that they seek, including build year, manufacturer, model, pump rating, water tank size and budget, to provide real-time information on vehicle availability that matches the criteria.Rebuilding existing rigs
The history of apparatus rebuilding can be traced back to the late 1970s, when many departments’ fleets suffered from premature rust and corrosion of the steel body and water tank components. During this period, hundreds of rigs were rebuilt with new aluminum or stainless steel bodywork along with upgrades to the pump, piping and warning lights. As new NFPA 1901 standards were introduced, canopy cab rigs were provided with four-door cab enclosures; eventually, steel cabs were replaced with aluminum four-door cabs to enhance crew protection.
During the latter part of the 1980s, inflationary pressures caused new apparatus prices to spike; several apparatus manufacturers required a down payment at contract or progress payments, as unstable material costs affected the industry. At the same point, NFPA 1901 changes for enclosed cabs and aerial ladder enhancements required the apparatus industry to redesign many of its products to comply with the new requirements. Fire departments were quick to assess their fleet to determine which units would make sense to rebuild to extend their life cycle.
Today, NFPA 1912: Standard for Fire Apparatus Refurbishing provides excellent guidance. This includes a detailed questionnaire to determine the extent of work that should be conducted on the apparatus, including to meet the requirements of NFPA 1901.
Before setting out to determine the extent of the project, five matters should be scrutinized.
Fleet options
Departments have had to adapt to economic pressures and budget constraints to maintain an acceptable level of fire protection for the community that they serve. The current fire apparatus market presents some challenges that chief officers and fleet managers must address.
The Apparatus Architects appreciate the assistance of James Wessel, who is the president and founder of Brindlee Mountain Fire Apparatus (Union Grove, AL), to help us to better understand the used apparatus market.
About the Author
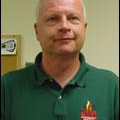
Tom Shand
TOM SHAND, who is a Firehouse contributing editor, is a 36-year veteran of the fire service. He works with Michael Wilbur at Emergency Vehicle Response, consulting on a variety of fire apparatus and fire department master-planning issues. Shand is a member of the Firehouse Hall of Fame.
Michael Wilbur
MICHAEL WILBUR, who is a Firehouse contributing editor, retired as a lieutenant in FDNY, where he was last assigned to Ladder Company 27 in the Bronx. He has served on FDNY's Apparatus Purchasing Committee and consults on a variety of apparatus-related issues around the country. Wilbur is a member of the Firehouse Hall of Fame. For further information, access his website at www.emergencyvehicleresponse.com.