Tour Highlights Pierce's Commitment to Design, Lifetime Service
Earlier this month, I went on a behind-the-scenes tour of the Pierce Manufacturing facilities in and around Appleton, WI. The media event coincided with the 9/11 Lambeau Field Stair Climb.
The tour included Pierce's Fabrication Products and Assembly facilities, the Neenah Assembly, and Oshkosh Airport Products Facility, plus Pierce Headquarters, the Pierce Training Center and the Product Lifecycle Support Center. Each tour was led by a different guide representing Pierce, from President Bob Schulz to Dan Meyer, the vice president of sales.
It began in the new boardroom at Pierce's Headquarters with welcomes and highlights from the 110-year-plus of history of the company.
As a first-time visitor at these facilities, here are some highlights and takeaways from the day.
Boardroom introductions
This is where Schulz emphasized how much Pierce values their employees and how tight-knit the company is. He added that they celebrate employees who hit 25 years of service, and every five-year mark afterwards. Pierce has two employees who have exceeded the 50-year service mark.
The two other focal points during the introductions were the priorities of company, along with how much responsibility Pierce takes on with each vehicle that they produce. The priorities of Pierce go in a very specific order: the first is safety, the second is quality and the third is delivery. They won’t compromise safety to make a delivery quicker.
“The oval on the front, we own it, end to end. If there’s a problem, we own it,” said Schulz. “At Pierce Manufacturing, we pride ourselves on what we call the 'Pierce Difference.' Our longevity in the industry, combined with our financial security, has allowed us to build a team of highly-skilled, tenured team members who are committed to excellence as well as continued investment in innovation, service, and capacity."
Over 100 Pierce employees are volunteer firefighters and having a personal tie to the fire service makes the work that they do just that more important.
Fabrication Facility and Neenah Assembly
This segment of the tour allowed me to witness the inner workings of how each cab is built and constructed. The detail that goes into each one of the apparatus is almost incomprehensible.
The 280,000-square-foot building was constructed in the 1970’s and it was expanded in 2002.
There are around-the-clock workers to ensure that orders get out on time. All the parts are made in-house, and finding the right part in the right place at the right time is crucial.
It takes about 80 hours to weld an average cab, and all parts are made in-house, except for the support castings. All apparatus are built twice from the ground up before the end of the building process to ensure durability and safety. There a multitude of reasons for why each apparatus is built twice. It involves making sure the paint doesn't get scratched when drilling holes, making sure the parts fit together and double checking all the work put into the apparatus.
Other fun facts:
- There are 369 different shades of red
- They have a jet that shoots at water at 90,000 PSI to help with cutting metal pieces
- Programming is done offline; workers can use an encrypted flash drive in case the system goes down
- For every three pumpers built, one aerial is built
- Hot slips, a slip that lets the workers know a piece needs to be built as soon as possible, allow for parts to be made in the same day, in just under four hours
There was also a section of this part of the tour that highlighted a welding training station.
Plant Manager Bill Kurtzweil was able to get Pierce to collaborate with high school students to allow them an opportunity to showcase their skills. There are 10 year-round welding apprentices that gives Pierce a “try before you buy” trial to see who can move up to the next level.
Oshkosh Airport Products
Before lunch, we took a drive over to the Oshkosh Airport Products facility where they produce apparatus for all seven continents. A showcase was given to the four Stiker Volterra electric ARFF rigs that pushses the Sydney, Australia airport's mission of being a carbon-free airport.
Rigs from this facility typically last 10-15 years, depending on usage and mileage. They work with the customers while they are there for the customers to see their apparatus and potetnially make changes. Ideally, it takes six weeks to produce an airport apparatus, three weeks to build and three weeks to test.
Assembly, Pierce Training and Product Lifecycle Support centers
The Assembly Facility tour was led by Meyer and Stephen Kohler, director of human resources, with Oshkosh Vocational. The tour took us around different parts of the building, such as the color room, the blue floor and shared stories from their years at Pierce.
The color room showcased the 981 and counting different shades of various colors, along with a showcase of how many different shades of red there are. Meyer said they, “make snowflakes at Pierce,” meaning, that no one apparatus is like another.
A story was told about how a captain and his team experienced a rollover in their apparatus, with parties surviving the crash. The captain was able to find the welder who worked on the cab that kept him and his crew alive. They even showed up to Pierce to thank the welder in person.
Service across the world
There are over 130 service centers for Pierce vehicles around the world, and those service centers serve as a big family business. Many service centers have multiple family members working there, or the businesses have been passed down from generation to generation.
“You don’t look for one part, you look for the best part,” said Kohler.
To enhance that notion, we were brought to the light tunnel that is exclusively a buffing station. Workers will sit there with heavy-duty lights to ensure there are no scratches on the apparatus.
We were brought to the infamous blue floor that is used for showcasing the completed apparatus to their customers. There is another blue floor being constructed to allow for enhanced efficiency and shows the development of Pierce, along with their patent wall. Pierce had four patents prior to being bought by Oshkosh, and now there are too many patents to showcase on the wall.
Next, we were able to get an inside look at the bottom of Pierce's totem pole, their training center which is home to various stations with real-life applications for the new hires that get hired every week. Each training station takes one week, and depending on development, training can last three to six weeks.
Last was a tour around the Product Lifecycle Support Center. This is where all the after-market products are held, and if there is an issue with a specific product on an apparatus, the team in this facility gets it fixed.
There is more than $16.8 million of value in products at the warehouse, and they work diligently to ensure the customers get their problems fixed. They ship 97-98 percent of orders on the same day, and ship about 400 orders per day.
Final Thoughts
Reflecting on the experience at Pierce, it was incredible. The amount of care, organization, and detail that goes into each apparatus will shock you. From graphics to welding to painting to testing, there are countless factors that go into creating such a high-quality vehicle that helps save lives.
“As a single-source manufacturer, we ensure that every aspect of our product design, manufacturing, and customer service is handled by one dedicated team. This approach, paired with the industry’s strongest dealer network and a comprehensive product line offering, allows us to provide unmatched support to our customers, backed by a warranty that reflects our confidence in our work. It’s this combination that truly sets Pierce apart and enables us to continue delivering reliable, innovative solutions for the fire service community. These are the aspects of our company which anyone who walks through our facilities will see firsthand,” said Schulz.
The job is important and goes under the radar. While there firefighters are the ones and facing the brunt of the danger, Pierce allows for those firefighters to do their job safely and efficiently.
About the Author
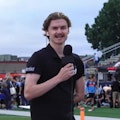
Ryan Baker
Ryan Baker is a writer and associate editor with prior experiences in online and print production. Ryan is an associate editor for Firehouse with a master's degree in sciences of communication from the University of Wisconsin-Whitewater. He recently completed a year of teaching Intro to Public Speaking at UW-Whitewater, as part of his graduate program. Ryan acquired his bachelor's degree in journalism in 2023 from UW-Whitewater, and operates currently out of Minneapolis, MN. Baker, also writes freelances for the Ultimate Frisbee Association (UFA) in his free time, while also umpiring baseball for various ages across the Twin Cities Metro Area.