Healthy Station Design Doesn’t End with Hot and Cold Zones
emoving carcinogens from a fire station requires addressing the two primary sources of carcinogens that are introduced to the station: those that are produced by fuel combustion that’s generated by vehicles that are inside of the station and those that are brought to the station from structural fires. Building code and Occupational Safety and Health Administration (OSHA) requirements are in place to meet the minimum acceptable levels for general air quality and work environment safety. However, additional methods are required to enhance users’ long-term health, safety and welfare and to prevent cross-contamination into living quarters and administration zones.
CO and toxin sensing
Apparatus bays have a general room exhaust system that’s code-required, and that system has an integral OSHA-required carbon monoxide/nitrogen dioxide toxin alert mechanism. This mechanism engages automatically when sensors in the system are triggered by CO or NO2 that’s present in the atmosphere of the bay. When the mechanism is engaged, air is extracted from the room and a louver system is opened to let fresh air enter into the space.
A toxin alert mechanism won’t engage every time, particularly not when apparatus bay doors are open or when a source-capture system is installed. Further, it isn’t designed to filter out carcinogenic particulates but merely to exhaust and replace interior air with fresh outside air. That said, utilizing it during the decontamination process assists the process and improves air quality in the apparatus bay. When vehicles are running indoors or when they return from a structural fire during the decontamination process, members should engage the room exhaust system manually. This will increase the efficacy of carcinogen removal.
A similar exhaust system has the possibility to be installed in some areas of the station that are not the apparatus bays. It can be used to sense increased usage by sensing carbon dioxide and/or movement within the space and then increasing the amount of fresh air that’s added into the HVAC system and, thus, replacing more of the air and refreshing the rooms. For example, installing this system in the turnout gear room and Hot Zone laundry/extractor/drying room could promote clean air in the spaces that might have built-up contaminants. In the administration and living quarters, installing a similar system in offices or bunkrooms will refresh the air in low-traffic areas. The use in private areas keeps air healthy and prevents staleness while personnel spend extended time in a small, confined space.
Because these spaces often are shared spaces throughout the week, use of such a system prevents unintentional cross-contamination of spaces.
Installing a sensor system would negate the need for staff to run the system. This can be coupled with a manual switch to run the system on demand or can be controlled by a time clock to coincide with shift changes.
HVAC
Air purification systems provide an alternate safety measure to fire stations to remove particulates from the atmosphere in lieu of, or in addition to, source-capture exhaust systems. The multistage purification systems can remove some gases, particulates and other contaminants, including viruses. The systems come in many sizes, forms and mounting system. Furthermore, they can be installed throughout the station, including apparatus bays.
The systems have several activation methods to make their function automatic, but again, having the capability to engage the system manually to use it during the post-structural fire decontamination process strengthens the measures.Importantly, these systems require regular maintenance and filter replacements. Station protocols should be expanded to include this. Fortunately, the unit will indicate when it needs filter changes.
Also, the quantity of the units that’s required to provide proper purification is based on the volume of the space, and an engineering team likely will need to be involved in coordinating proper installation.
Installing an air purification system in other parts of the station might not be directed to remove carcinogenic particulates but can improve the air quality of living and administration spaces. Because the system is set up with multistage filters, it removes many types of pollutants, large and small. This can keep the air that’s in other areas of the station clean.
Placing these units in shared areas can clean shared air, possibly eliminating odors/dust and reducing sick time for personnel.
Some of the common areas that might be recommended for installation of these systems include lobbies, training rooms, conference rooms, shared offices, locker rooms, kitchens and dining rooms, day rooms and exercise rooms. Furthermore, the systems can be installed above ceilings for areas where aesthetics is important.
To further address the removal of carcinogens in the station, reiterating and strengthening the Hot Zone design and NFPA requirements and protocols are critical. Preferably, the hypothetical goal is that, during the decontamination process, the living quarters and administration zones (i.e., Cold Zones) remain isolated, or “out of bounds,” until the process is complete.
Designing an HVAC system to provide positively pressured clean air in the transition and clean zones allows the system to prevent the contaminated air from entering the Cold Zones. However, from our group’s recent experience, many users reported that protocol often is broken by a member’s trip to the restroom after that individual returns from a call. Additionally, this breakdown typically includes the lack of handwashing prior to use of the toilet.
Decon rooms & showers
Finding a balance of decon rooms, toilet rooms, and Cold Zone shower or locker rooms and toilets is essential to the cost, space, and proper sequencing of health and safety protocols. The incorporation of an additional single-user toilet that’s located directly off of the apparatus bay in the Hot Zone might be necessary to prevent contamination of the Cold Zone.
Also, adding to the quantity of decon rooms that are located off of the apparatus bay allows more than one firefighter to decontaminate at a time. This affords a quicker turnaround for the firefighters.
The downsides to adding multiple decon rooms are increased cost and use of prime space, in particular. However, additional Hot Zone showers could be offset by reducing the number of Cold Zone showers, because all of the Hot Zone showers can be used as Cold Zone showers once they are cleaned. As well, perhaps other carcinogen-exposure-reduction methods can be foregone in station planning entirely, giving room for additional decon showers and cleaning procedures.
Handwashing stations
Increasing the number of handwashing sinks in and around Hot Zones and directly adjacent to access to the Cold Zone should be considered mandatory.
Both infection control and decon procedures call extensively for washing with water of persons (and equipment), although this protocol often is foregone for the easier step of hand sanitizers and cleansing wipes.
NFPA standards are very clear that using hand sanitizers and cleansing wipes is a temporary stopgap to the vital rinsing away of particulates with water and detergents, preferably as soon as a handwashing basin or sink fixture can be accessed. Hand sanitizers and cleansing wipes might antisepticise most diseases and viruses, but the same can’t be said for neutralizing carcinogens.
Ideally, every time that users return to a Cold Zone, having done something as minimal as picking up a tool or touching a wall—not to mention returning from a call—they should wash particulates from their hands before entering and touching items in the Cold Zone. This task can’t be performed easily when proper equipment isn’t made convenient for them.
Vehicles
Washing contaminated vehicles outside of the station redirects particulates, and components of the apparatus bay washing systems, such as warm water hoses and exterior storage systems, can translate themselves easily to the exterior to facilitate that redirection of particulates.
The amount of fuel-combustion carcinogens that’s generated in the station can be reduced by utilizing electric or hybrid vehicles, which can enter and leave a station without producing combustion. Although it’s excessive to believe that an entire fleet will turn over to electric or hybrid vehicles in one swoop, stations can start to prepare for these vehicles by introducing the correct power source to handle the future electric load; preparing secondary spare panels and spaces for future generators; and running empty conduits to the stalls in the garage and on site for the vehicles.
Commitment
At this point in time, until more evidence is presented to all of us, further diminishing of the cancer risk within the firehouse comes down to design and equipment enhancements, ever-improving protocols and procedures, and making those actions habitual.
This article is part of the Station Design Supplement 2023. The entire supplement can be found here.
Can Saunas Reduce Firehouse Carcinogens?
Some stations are installing saunas and heat exposure exercises for post-structural fire exposure to carcinogens in hopes of reducing the amount of carcinogens that stay on or within the body. However, as discussed in “Evaluation of Intervention to Reduce Firefighter Exposures,” which was published in the Journal of Occupational and Environmental Medicine (JOEM) in April 2020, a study of specific interventions that are used by the fire service to reduce or mitigate exposure to carcinogens found that the use of infrared saunas after exposure to carcinogens has “non-significant reductions” in the output of carcinogens through urinary testing. Furthermore, the article specifically mentions the potential to cause harm to the cardiovascular system through heat stresses. However, the study didn’t test that claim specifically, and the study authors admitted that more research must be performed to test the hypothesis.
Therefore, the installation, upkeep, maintenance and use of these heat exposure elements and spaces, not to mention the procedural time that’s devoted to these protocols, is forecasting in early studies to be futile.
About the Author
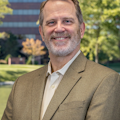
Mark Bushhouse
Mark Bushhouse joined Williams Architects in 1987 and is a licensed architect in several states. While leading the firm as president, he also oversees its municipal and interiors practices. Bushhouse has full project architectural responsibilities, with a focus on master planning. He practices project leadership, planning expertise and effective cost control, which allows the team to create realistic, cost-conscious solutions for clients.