Fire service history tends to repeat itself, and this is often noted with current trends in fire apparatus design. As each new year brings technological advances in components—including pump panel electronics, foam systems, cab safety equipment and aerial ladder designs—some, but not all, of these advances are easily embraced by fire departments. New technology often comes at a cost and complicates vehicle maintenance with a reduction in in-service time.
Safety and size
Without question, today’s vehicles are safer due to the impact of NFPA standards, along with the increased use of seatbelts, airbags and rollover protection. This is reflected in a reduction in the vehicle-related line-of-duty deaths from 19 in 2012 to six in 2015.
Further, beginning in 2005, most manufacturers initiated the process to redesign their cabs to accept the next generation of EPA-compliant, lower emissions diesel engines. These changes resulted in wider cabs or reduced space in the front for the driver’s and officer’s seating positions. When combined with the need for increased storage space inside of the cab for EMS equipment and other gear, the interior space can become cramped in short order.
Tool and equipment storage can be a complex issue to address when designing new apparatus. It is important to discern at the beginning of the specification process exactly what the primary mission of the vehicle will be. This will help determine the extent of the tool and equipment cache that will need to be carried, and is critical when outfitting a combination apparatus, such as a rescue/engine and quint where cab and compartment space are limited. While the NFPA 1901 standard allows for a weight of 250 pounds per seat for personnel, the size and number of interior compartments, door configuration and equipment carried all have an impact on the front-axle loading and, ultimately, vehicle performance.
There is little doubt that apparatus manufacturers have approached the practical limit of physical cab size and weights that can be safely engineered on a single-axle chassis. Department demands for larger fire pumps, water tanks and equipment storage have resulted in many vehicles with gross vehicle weight ratings approaching 55,000 pounds on a single axle. The result is often an apparatus that met all of the fire department’s requests, but is too large for the response district and does not perform any particular function very well.
Engine apparatus design is highly geographically dependent, with many West Coast engine units being shorter in wheelbase and overall length, with particular attention paid to the angles of approach and departure. This is partially due to more stringent state weight regulations that are enforced on all vehicles, including fire apparatus. Apparatus deployed as a part of a wildland strike team must be capable of traversing on all types of terrain. For this reason, West Coast engine apparatus have a distinctive appearance to meet the intended mission.
One trend that seems to have taken hold is that many departments are returning to more modest size engine apparatus when compared to vehicles that they are replacing. Urban departments have dealt with fire stations with limited apparatus bay space, congested streets, double-parked cars and other obstructions. Engine apparatus in FDNY, the District of Columbia and the City of Los Angeles have been designed to meet the mission and still be modestly sized. Short wheelbase apparatus with low rear hosebeds, exposed ground ladders with tools and equipment located so personnel do not have to climb on top of the apparatus are gaining favor with many departments.
Fire pump controls and panel designs
Fire pump controls and panel designs have evolved over the years, with the inclusion of foam systems, electrically controlled discharge valves and remote-controlled deck guns. Let’s look at each area to assess its impact on vehicle cost and daily operations.
Foam systems—from basic bypass foam systems with ratings up to 125 gpm to the fully electronic dual-agent foam systems—can be integrated into most pump configurations. Depending on your department’s response district and past experiences with Class A foam, this hardware can be vital. Departments that routinely utilize Class A foam for structural and wildland firefighting have very positive results with these systems and would not purchase an apparatus without a foam system.
Depending on the frequency of use in training and daily operations, the flip side of foam systems are that some apparatus committees fall into the trap of specifying the most complex and expensive system simply to put it on the new rig, with no forethought as to the impact on vehicle operation and testing required to properly maintain the foam system equipment. There are few components on a fire truck where the words “Foam System” can result in a cost increase anywhere from $3,500 to $65,000.
The use of electrically controlled intake and discharge valves has increased, permitting more compact-size pump panels with flexibility as to the position and location of the valve and associated pump plumbing. Some vehicle configurations, such as mid-mount tower ladders equipped with a fire pump, require the use of electric valves due to the room available to mount the pump and discharge piping. Reliance on this technology comes with a price, as the components are considerably more expensive than a traditional direct-acting linkage on a 2.5-inch discharge. The trade-off here is cost vs. convenience, understanding that if the valve is controlling a critical function, such as a tank to pump line or discharge with a preconnected attack line, these valves should be provided with an easily accessible manual override.
Remote-controlled master stream devices permit operation from the ground, without having to commit personnel to the top of the apparatus. Fire departments should review the number of incidents where heavy stream appliances were deployed and the engines were properly positioned on the initial response. Manually controlled deck guns or the use of portable ground monitors that can be preconnected to hosebed lines and deployed by one person may provide more flexibility with your engine company operations.
The pump panel configuration and layout can be reviewed and finalized at the pre-construction conference. Most apparatus manufacturers have a standard pump panel that they would prefer to provide where instrumentation, intake and discharge locations are predetermined by engineering. This may work for some departments; however, the pump panel area should be consistent with your other engine apparatus with similar locations for the major components. Specifying 6-inch master gauges and 3.5-inch individual discharge gauges can make the pump operator’s job much safer and easier. Options such as backlit gauges and flowmeters may be of some benefit, but again all come at a cost and are not free. Flowmeters, like foam systems, require calibration and maintenance and over the life cycle of the apparatus will increase operational costs.
Pump governors are almost standard across the enterprise and provide features such as preselected pump pressures, cavitation protection and engine monitoring systems. Depending on which era your fire service career started, you may have trained and operated a pumper equipped with a relief valve and Vernier throttle. These components were very reliable but over time fell out of favor to the electronic pump governor. It is always interesting to see an old school pump panel with manually controlled discharge valves and a relief valve with a well-trained operator and crew that can move water without delay.
Corrosion issues
Departments that operate in the Northeast and snowbelt areas of the United States must deal with rust and corrosion as the result of road deicing chemicals. While galvanneal bodies can be specified by some departments, the use of aluminum and stainless-steel body material is critical to providing the needed vehicle life cycle. Several manufacturers are offering different corrosion-control treatments for the chassis frame rails, cross members, air reservoirs and other steel components that are susceptible to damage from rust and road chemicals. While the cab and body compartment construction are more resistant to corrosion, the vehicle chassis frame and body sub-frame are more susceptible to corrosion damage and may require restoration and repairs in order to provide 10 to 15 years of front-line service.
In sum
Developing apparatus specifications that meet the operational needs of the fire department can be an arduous task. Careful planning and discussions with the apparatus committee, including maintenance personnel, will result in a well-designed vehicle that will provide years of reliable service.
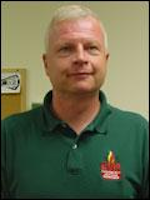
Tom Shand
TOM SHAND, who is a Firehouse contributing editor, is a 36-year veteran of the fire service. He works with Michael Wilbur at Emergency Vehicle Response, consulting on a variety of fire apparatus and fire department master-planning issues. Shand is a member of the Firehouse Hall of Fame.