Given today’s budget environment, equipment repairs can be especially painful. Equipment never seems to break down when coffers are full; rather, it seems that “Murphy’s Law” waits to take effect until there are no available funds. The unpredictability in both frequency and associated costs make maintenance budgets erratic and difficult to plan accurately.
This can be particularly painful for critical equipment. Even though the cost of repair may be high, doing without the equipment is often times not desirable, so the chief has to once again find a way to come up with the money. While there is no way to guarantee that “Murphy” won’t come calling; certain things can be done to help keep “Murphy” at bay and even potentially improve the performance of your thermal imager.
• Operational checks – Many departments, as a part of daily apparatus checks, turn on the imager to make sure it is still operational. However, simply turning the imager on, seeing if an image is displayed and then turning it off again offers no real assurance that all is OK. In fact, this type of “check” may actually do more harm than good. The act of taking the battery off of the charger, drawing a very small amount of power from it and then placing it immediately back into the charger can decrease the performance of the battery over time. If the imager was operational when it was returned to the charger after the last use, turning it on is no guarantee that it will turn on the next time. If you are going to perform an operation check of the thermal imager each morning, then really check its operation.
Turn it on and check the image quality. Is it in focus? Focal distance for most thermal imagers is about three feet out to infinity. If an object 10 to 15 feet away appears blurry, then it is possible that the focus needs to be adjusted. While it is unusual for an imager to be out of focus, it is not unheard of.
Check the image for clarity. Is there any noise in the image? Noise looks a bit like background static. It is typically fixed and does not change location as the imager is moved.
Does the temperature measurement respond? Does the color activate as expected? Does the imager shift from high gain to low gain appropriately? All three can be tested with a stove. If you have a gas stove, a frying pan helps the process along. Turn on the stove and check that all works as expected. If there are any other features of the thermal imager or accessories attached, then make sure these operate as well.
• Power management – A frequent source of complaints about imager performance is power. Maybe the batteries don’t run long enough, don’t last long enough or don’t charge fast enough. While the issue of battery maintenance is too complex to cover in this column, there are ways to help your batteries perform at peak levels, regardless of physical condition. When you get a new battery, check the label for a date code. If it is missing, add one. It is nice to know how old a battery is since all batteries have an expected operational life. While this operational life is variable, age of the battery can help you identify a typical life span for your department so that you begin to predict and plan a replacement cycle.
Check the battery casing for damage. Damage such as cracks in the case can indicate a severe impact and may let dirt and debris get into the battery. More subtle damage such as swelling of the plastic can indicate a failure mode in the battery where the internal temperatures of the battery are getting too high during charging or use. All you will notice is that normally flat surfaces of the battery appear “domed.” This is different than external heat damage, which will normally appear bubbled or melted. Batteries that appear swollen should be removed from service because they can fail without warning.
Pay attention to the chargers as well. Look for dirt or debris on or around the charging contacts. Check the power source for the charger (wall adapter or vehicle plug) for signs of swelling or damage to the wire. Check the contacts of the charger and batteries for signs of corrosion or grime buildup. You can clean most battery contacts with something as simple as a pencil eraser. If it takes something more abrasive, a 220-grit sandpaper will also work. Be careful not to apply so much pressure that you damage the contacts. Never use steel wool as this can bridge the contacts of the battery or charger and cause serious damage. When working on the charger, you should always remove it from the power source for safety.
• Cleaning and inspecting – Inspect the outside of the imager for damage and cleanliness. Your thermal imager should always be kept as clean as possible. The shinier the surface of the imager, the more radiant heat the imager will reflect rather than absorb. Excessive soot buildup will lead to higher absorption of radiant heat and will affect how long the imager may run in an extremely hot environment.
Simple cleaning can be performed with soap and water. More stubborn stains can be safely cleaned with common, household cleaners or degreasers. Never use straight bleach or hydrocarbon-based solvents on your thermal imager as these products may harm the thermoplastic housing or rubber seals. Always consult your owner’s manual or contact the manufacturer to check on recommended cleaning agents.
Once clean, the imager will be easier to inspect visually. When inspecting the imager, look for cracks in the plastic of the outer shell as well as any separation in external components. Also inspect all rubber or neoprene checking for pliability, crumbling, tears or other visible damage. Cracks, separations or damaged seals are common causes for water intrusion into the imager. Although all thermal imagers on the market today are IP67-rated (waterproof for 30-minute immersions in three feet of water) or better, this is only true when the imager leaves the factory. What happens after that is an issue of use and maintenance. There is nothing magic about the electronics of a thermal imager; there is magic only in the way they are protected from the harsh environment of firefighting. Water intrusion can lead to costly repairs, so frequent inspection is the best way to avoid this.
• Lenses, windows and display covers – An often-overlooked area of maintenance is the lens or window at the front of the imager. These areas can build up some very tough stains and will directly affect image quality. Most optics used in thermal imagers today are made of germanium. Germanium is a crystalline mineral that happens to be highly transparent to infrared energy. The germanium is often cooler than the firefighting environment because it has the internal air inside the imager behind it. This makes it susceptible to condensate from the environment resulting in buildup of soot and creosote. This buildup can reduce the amount of thermal energy getting into the imager, reducing overall picture quality as well as creating a blurry appearance of the image. Cleaning this area of the imager can be extremely difficult. Contact the manufacturer for suitable cleaners and/or solvents. In some severe cases, replacement may be the only option.
When a thermal imager breaks down, it can be both costly and inconvenient to repair. Although all imagers will eventually break down, the useful life can be extended and repairs avoided or minimized through a routine method of thorough inspection and immediate remediation of the small issues.
Recognizing and mitigating small issues can prevent the development of more expensive repairs. If you have questions about inspection or repair issues specific to your thermal imager, please contact your manufacturer.
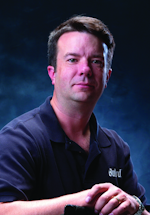
Brad Harvey
BRAD HARVEY is the Thermal Imaging Product Manager at Bullard. He is a veteran of public safety as a firefighter, police officer and paramedic and is certified through the Law Enforcement Thermographers’ Association (LETA) as a thermal imaging instructor. Harvey has worked as a high-angle rescue instructor and is a certified rescue technician and fire instructor. If you have questions about thermal imaging, you may e-mail him at [email protected].