Apparatus Innovations: The Evolution of Aerial Device Controls
Aerial devices, whether a ladder, a tower ladder, an articulating boom, an elevating waterway or any other type, all have a hydraulic system at their core. However, the controls of one aerial device might vary from those of another.
Direct hydraulic control, which often is referred to as a manual hydraulic system, is the oldest type of aerial control. With direct hydraulic control systems, the operator’s control levers are connected directly to a hydraulic valve that controls a given function. Whether it’s outrigger or aerial function controls, when the operator exercises a lever to perform that function, the operator physically is opening or closing a valve. (The most common aerial operator controls are lever controls, but pistol-grip controls are available from some manufacturers.)
As technology has progressed, electric control systems of aerial devices have become common. These systems use electronic solenoids to open and close hydraulic valves. The solenoids are controlled by electric signals that are sent from conventional lever controls, push-button switches, paddle switches or joysticks. Some systems might be a simple open or close operation; others systems allow for “feathering” of the hydraulics to control speed (think of the way that a dimmer switch controls lighting intensity).
Some aerial device hydraulic systems might have a combination of functions, some of which are direct hydraulic control and others that are electric-over-hydraulic.Nuanced improvements
The hydraulic systems of aerial devices have had many subtle refinements incorporated into them over time, and these refinements have made the apparatus operator’s job seamlessly easier.
The basic system still is a reservoir, a positive displacement pump, a high (supply) and low (return) pressure plumbing system, filtering and valves to control various functions.
There was a time when the aerial operator had to close a manual valve to shut off flow to the aerial lift cylinders to lock them in place prior to anyone climbing the aerial. Those manual valves were replaced by dual pilot-operated check valves that shut off flow to the lift cylinders when the raise/lower control is placed in the neutral position. This automated safety feature reduced the number of functions that the operator must complete.
The aerial operational requirements of the 1991 edition of NFPA 1901: Standard for Automotive Fire Apparatus state that the aerial device must be capable of operating and supporting its rated tip load in its entire operational range, fully extended, with stabilizers fully deployed. This is accomplished easily with both manual hydraulic controls and electric-over-hydraulic controls.
The use of manual hydraulics for outriggers and at the turntable is accomplished simply for all aerial devices. However, electric-over-hydraulic controls for platform controls for a tower ladder and for creeper controls at the tip of an aerial ladder are used because it isn’t feasible to run hydraulic lines up the aerial devices. Variations exist between the different manufacturers, so extensive research must be done to choose the system that’s best suited for a department.Significant options
Numerous new features that owe their development to electric-over-hydraulics are being built into many aerial devices.
Short-jacking is virtually seamless to the operator for the duration of the fireground operation unless the operator tries to rotate the aerial device to the short-jacked side of the apparatus. This would cause the safety limitations of the system to be activated. Otherwise, there isn’t any operational limitation when the operator keeps the aerial device on the fully deployed stabilizer side.
Auto-leveling is gaining popularity, but it requires additional controls at the outrigger station. Auto-leveling can be overridden by using the regular outrigger controls, so it doesn’t present any limitations if for some reason it doesn’t work correctly.
Aerial devices now can be programmed to avoid accidental contact with the apparatus cab, the compartment body and other body-mounted obstructions. This is accomplished because of input from sensors and electric-over-hydraulic controls. It does increase the amount of electronics on the aerial device and the hydraulic system.
The 2009 edition of NFPA 1901 allows for “envelope controls” to be installed on aerial devices. These are a carryover from the crane industry, but from the operator’s point of view, very few differences are noticeable in the system of an aerial device that has envelope controls compared with an aerial device system that lacks them. However, the internal workings of the aerial device are quite different.
Envelope controls are electric-over-hydraulic systems that are heavily computerized. Sensors on the stabilizer system and on the aerial system constantly monitor outrigger deployment status, aerial device operating angle, extension and rotational position, and tip load. The information that’s collected is both broad-based and detailed. For example, the control system knows when the apparatus is short-jacked as well as by how much the apparatus is short-jacked. The control system knows how much the aerial device is extended and at what angle it’s operating. The system processes real-time operating parameter data. The control system decides where the aerial device can and can’t go in operating range based on the information.This operating system is markedly different to what the fire service is accustomed. Much training and practice on the part of an operator is required to really understand the benefits and limitations of this system.
The newest innovation was introduced in 2021. It also is an envelope control system that’s based on an electric-over-hydraulic system. It also is heavily computerized and has a sensor array on all parts of both the stabilizer system and the aerial device. In fact, there is very little difference in the appearance of this aerial device and its operational controls from the aforementioned envelope control system.
The difference lies in the way that operational limitations are handled. Instead of limiting where the aerial device can go based on data input, this system allows the aerial device to go anywhere in its operational range. Such a circumstance is more in line with the operational characteristics of an aerial device that so much of the fire service is accustomed to.
What is limited is the tip load. The tip load—along with the stabilizer spread and aerial operational angle and extension— is monitored constantly. When the system recognizes that the operator is moving from an operational zone where the tip load is rated high to an operational zone where the tip load is rated lower, the aerial stops, and the operator must acknowledge the reduction in tip load to continue to operate. If the operator moves from an operational zone where the tip load is rated lower to one where the tip load is rated high, the aerial device continues to operate with no interruption.
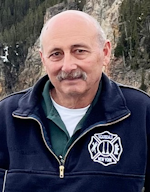
Jeffrey D. Gaskin
Jeffrey D. Gaskin is president of Big Red Trucks Fire Apparatus Consultants. He is a retired captain from the Scarsdale, NY, Fire Department. Throughout his career, Gaskin has been involved in apparatus acquisitions, from needs assessment through specification-writing. He also is a fire apparatus mechanic and holds certifications from Allison Transmission, Detroit Diesel, Hale Pump, Smart Power, Spartan Chassis, Sutphen Fire Apparatus and others. Gaskin is certified by the Emergency Vehicle Technician Certification Commission in six areas: Fire Apparatus Inspection, Maintenance and Testing (F-1); Design and Performance Standards of Fire Apparatus (F-2); Fire Pumps and Accessories (F-3); Aerial Fire Apparatus (F-5); Allison Automatic Transmission (F-6); and Hydraulic Systems (F-8). He can be reached at [email protected].