Fire apparatus has evolved to a point where, in some instances, we are operating vehicles that are pushing the legal weight limits imposed for interstate highways. Vehicle dimensions, such as overall length and height, have become so large that the vehicle’s physical size has made it difficult to work from, with attack lines and equipment that are literally out of reach of the average firefighter. Further, recent anthropometric studies have concluded that 95 percent of firefighters do not fit well into current cab seating, which also impacts the position and location of handrails and stepping surfaces.
The multi-purpose approach
We can all probably remember viewing a piece of apparatus that was on display at a local fire show and thinking to ourselves, “Why on earth did they do that?” The level of customization on fire apparatus is largely dependent upon the perceived needs of the department as well as the manufacturers’ ability to develop new and innovative components that catch our attention. While not to demean their capabilities on the fireground, combination apparatus, such as rescue engines and quints, have fostered the concept that departments can combine a number of components, tools and equipment into one vehicle that will bring the entire toolbox to the incident. As a result, many all-hazards agencies have embraced the multi-purpose apparatus as the answer to their needs to carry the majority of their equipment on a single unit. The question then becomes when does a piece of apparatus become too large and cumbersome to operate, either within the first-due area or in other neighboring jurisdictions.
In part, the size of apparatus is related to our staffing models and deployment practices. Where many departments are fortunate to provide four-person staffing on engines and trucks, all too often we operate with less-than-optimal staffing, which results in five to six units at the scene with 12 personnel tasked to do everything. This common scenario has caused some departments to acquire multi-purpose apparatus to carry more tools and equipment on a single unit, as staffing does not permit the response of other vehicles. These combination units may work well in wide-open areas in front of strip malls, but in some communities, the square footage of residential homes has grown to the point where the life safety and fire potential is a greater concern. This is further complicated when roadway access for apparatus is limited due to driveway layout, grades and decorative stonework. More than ever, apparatus committees must evaluate the service needs of their first-due areas and temper this with some practical application of situational awareness to provide for a well-designed apparatus.
Weight issues
The NFPA 1901 standard in Table 12.1.2 provides some excellent guidance as to the minimum equipment payload weights that should be considered for the various types of apparatus. For example, for pumpers with enclosed compartment space of less than 250 cubic feet, the minimum equipment allowance is 2,000 pounds and increases to 2,500 pounds for larger bodies. As these payload allowances are a minimum, the fire department must clearly identify their requirements for hose, tools and appliances when developing their specifications. Combination apparatus such as rescue-engines and single-axle quints are particularly vulnerable for being overweight if the equipment weight has not been determined early in the process.
Overweight fire apparatus is not limited to combination apparatus or any particular style of vehicle. Unfortunately, there are many pieces of apparatus operating today that are overloaded, as the equipment complement was not specified and, over a period of time, additional tools were mounted on the apparatus, potentially resulting in poor braking and vehicle performance. Over the past three years, as a result of numerous fleet studies, many departments have been surprised to learn that after each of their units were weighed on certified scales, one or more vehicles were overweight, in some cases with no personnel on board. Some units had to be taken out of service, with changes ahead in equipment and hose complements, reduction in water tank size or new axles, tires and suspension components installed.
During the specification-development process, the apparatus committee should review the tool and equipment requirements, starting with an inventory of existing apparatus. While the NFPA 1901 standard lists basic equipment requirements for engine, ladder and special service units, this equipment loading typically does not capture all of the tools and appliances that departments will require on their front-line units. For example, it is one thing to call for a hydraulic rescue tool compartment to include reels and sufficient slide trays to accommodate fire department supplied equipment and another to detail the specific make, model, size and weight of this equipment to ensure that sufficient compartment space and weight is available to safely carry these tools.
Dimension details
Most apparatus manufacturers have developed body designs with specific compartment dimensions based upon the capacity of the water tank and hosebed to provide different lengths in order to meet fire departments’ needs. The apparatus committee should inquire as to the various options to determine the best match for the overall length of the body and how this may impact the wheelbase and turning radius for the completed unit. Departments often simply choose the largest body size available and then work backward to make the tools and equipment fit within the available space. This often results in mega-sized apparatus that carries everything but does not allow access to tight areas within the community or simply cannot maneuver in locations where older vehicles could easily fit.
When reading through manufacturers' specifications, remember that all dimensions are not necessarily equal. Some specifications state the overall compartment dimensions in inches for the height, width and depth of each area. These numbers, while impressive, may not take into consideration the loss of height due to headers or the roll-up shutter and the clear door opening past hinged doors or trim pieces. In addition, the depth of each compartment should be the clear useable space for equipment storage with the door closed. The use of slide-out trays for easier access to equipment must allow not only for the height of the slide mechanisms and thickness of the tray itself but also the side clearances required to pass through the door opening. Some of these dimensions are not normally provided in specifications provided by the apparatus manufacturers and will have to be determined after consultation with sales personnel and their engineering staff.
After the specific compartment dimensions are established, you can begin to lay out your tools and equipment within each compartment area. If you have already developed the apparatus inventory of equipment, including dimensions and weights, there are several methods that you can use to lay out each compartment shelf, tray and tool board space. Several manufacturers and equipment mounting companies can provide a computer-aided drawing (CAD) for each area within the compartment body.
These CAD drawings can be of great assistance before any metal is sheared to ensure that your equipment can be safely mounted in each location.
Another technique that can be accomplished in the fire station is to mark out on the apparatus bay floor with tape each surface area, such as an adjustable shelf, tray or wall area, and locate the desired equipment within the space. Documentation of this work should include digital images and a listing of the appliances and equipment for each location.
The work conducted at this point in the design process can alleviate some of the issues that crop up later and can cost a great deal of time and money to solve once the apparatus goes into production. This work is particularly important if your department is designing an apparatus that is will combine the equipment from several pieces of apparatus into a single unit. The apparatus manufacturer will be able to validate your requested tool and equipment locations while providing an accurate analysis of the anticipated in-service weight of the apparatus prior to construction. Failure to provide this level of detail during the design phase can lead to unbalanced side-to-side weight or overloaded apparatus that, in some cases, cannot be easily modified for overall vehicle safety.
Sample text
One of the requirements within the specification boilerplate should be for each bidder to provide a detailed weight analysis of the apparatus as proposed. This analysis would provide information on the front and rear axle loading based upon the weight of the equipment provided by the fire department. This analysis would then be compared to the actual vehicle weight when delivered to the department and, prior to acceptance, the vehicle would be weighed with all hose, tools and equipment to ensure that the vehicle is within the rated axle and chassis gross vehicle weight rating (GVWR). Typical specification verbiage would read as follows:
“Each bidder’s proposal shall provide a complete weight analysis indicating the estimated front- and rear-axle weights for the loaded vehicle including full fuel, water and foam tanks, six (6) personnel, the specified hose load and a minimum of 2500 pounds of tools and equipment. This analysis shall detail the weight of the major components, hose and equipment showing the weight applied to each of the vehicle axles. A general statement indicating the front and rear delivery weights from the factory shall not be considered as acceptable.”
While tool and equipment mounting is one of the last items to accomplish prior to placing the unit into service, you must give consideration to how this work is going to be conducted. Some departments have historically left this work to the individual fire companies, with mixed results. Others have tasked this work to be conducted by the department shops and mechanics to provide some standardization in tool and equipment placement. Apparatus committees should consider including a specific amount for tool and equipment mounting into the final specifications to ensure that the complete inventory will be properly and safely secured in the cab and body compartments. A statement similar to the following could be included:
“Each bidder shall include an amount of seven thousand dollars ($7000.00) for tool and equipment mounting of fire department supplied equipment including hydraulic rescue tools as listed in the attached specifications. The tool mounts, whether custom fabricated or commercially purchased hardware, shall be approved by the fire department. All tools shall be made available to the successful bidder after completion of the final inspection and shall be mounted under the supervision of the fire department prior to final acceptance and payment for the apparatus.”
When working on new apparatus specifications, the department should develop a complete equipment inventory, plan the space allocation needed to safely accommodate and secure this equipment. Don’t fall into the common trap of acquiring the largest body style available with the hope that everything will work out. Considering the life cycle of the apparatus, while leaving some open space for future equipment, the cost of tool and equipment mounting is nominal when compared to some of the more costly components that are installed on new units.
Careful planning pays off
With the increasing services provided by many departments, the apparatus compartment space can be at a premium within a short period of time after placing the vehicle into service. Careful planning during the specification process, including developing the hose, tool and equipment inventory, will reduce the likelihood of your department ending up with an oversized apparatus with weight and performance issues.
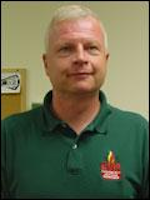
Tom Shand
TOM SHAND, who is a Firehouse contributing editor, is a 36-year veteran of the fire service. He works with Michael Wilbur at Emergency Vehicle Response, consulting on a variety of fire apparatus and fire department master-planning issues. Shand is a member of the Firehouse Hall of Fame.