The Apparatus Architect: Apparatus Purchasing amid COVID
During the past year, fire departments across the country had to adjust their operations because of the pandemic and its effect on their community. In addition to having to protect members with enhanced PPE, many departments changed response protocols in an effort to reduce the number of units and personnel that could be exposed to the virus.
Others altered shift schedules with increased overtime costs. In some cases, fire rescue services continue to be provided despite reduced funding.
Community shutdowns will have a long-term effect on financial resource allocations for fire rescue organizations, including a reduction in funding for capital projects. This ultimately might affect apparatus replacement programs. For departments that are fortunate enough to have secured funding for new apparatus, the apparatus purchasing process has changed dramatically as a result of the pandemic.
Historically, the apparatus procurement process involved a number of department personnel, including chief and company officers, drivers/engineers and fleet maintenance. At times, face-to-face meetings would be conducted with apparatus manufacturers’ representatives to identify design criteria that would be used to develop specifications. Committees would travel to see newly delivered apparatus that were similar to their requested design and would attend fire conferences to meet with component and equipment vendors to network and gain technical information.
Most, if not all, of the past practices have been put on hold because of the pandemic and associated travel restrictions. What should apparatus committees that are working on new rigs for their departments expect during the coming months?
Bid process
Conducting committee meetings in many instances will be accomplished using Zoom or some other platform to enable members to remain safe while exchanging ideas and developing requirements for the new apparatus. At this point, if the department needs to obtain competitive bids, someone on the committee must develop the specification or utilize the resources of an outside consultant to assist the group with this task. Agendas must be established for each of the remote meetings to keep the project on task as well as to set the priorities and timetable for specific benchmarks.
As an alternative, the department may choose to utilize one of the nationally recognized purchasing consortiums, which enables the committee to choose a specific manufacturer and base model and to identify all of the specific components and design features on the vehicle. In this instance, the local manufacturer’s sales representative can provide information on available configurations or suggest a similar apparatus that has many of the desired features. Although this process eliminates the need for the committee to produce a detailed specification and can reduce the amount of time that’s needed to confirm an acceptable design, there are some details that must be addressed prior to going to contract with the preferred vendor.
Apparatus committees that fail to adhere to the following guidelines end up frustrated at the pre-construction meeting, resulting in extensive change order and associated increased expense:
It is more vital than ever for all committee members to thoroughly read and understand the long-verbiage specifications for the vehicle, as this is the legally binding document that governs the construction of the apparatus. In the past, the Apparatus Architects have observed that only a few committees take the time to read the document, which can run more than 130 pages.
A detailed tool and equipment list, including weights, must be developed and shared with the preferred manufacturer, including the required hose load and ground ladder configuration.Prior to contract, the committee should insist on obtaining the following documents for review and approval to confirm that the vehicle as proposed will be operationally safe: detailed weight analysis, electrical load analysis and turning radius diagram.
Working with the preferred manufacturer, the committee should review and determine the desired dash panel and switch locations, pump panel color coding and body compartment layout, including trays, shelves and other components.
Ensuring that these areas are addressed will make the pre-construction meeting, whether virtual or in-person, move along smoothly and enable the group to concentrate on other details of the production process.
Pre-construction, manufacturing
Historically, the fire service has been accustomed to being able to place an order for a new apparatus and have the vehicle delivered within 10–12 months. The pandemic has affected the manufacturing sector in many areas, including lost time because of employee illness, vendor component delivery issues and extensive changes to vehicle design that result from the pre-construction meetings. All of these result in extended delivery times, particularly for high-input-hour units, such as heavy rescues and aerial devices. Now, departments should plan on 12–14 months from the time of contract to delivery of their new rig.
Many apparatus manufacturers now quote delivery time that’s based on customer sign off of the change order and revised blueprints after the pre-construction meeting. Depending upon the backlog of new orders with your preferred manufacturer, it might take more than 90 days after contract award to reach this benchmark in the production process. Unless your organization is in immediate need of a replacement apparatus because of accident or some other unforeseen event, the apparatus committee should expect an extended delivery period and consult with your sales personnel to determine what a realistic delivery time frame would be for your new vehicle.The Apparatus Architects have advocated to have the pre-construction meeting at the manufacturer’s facility. This enables the committee to view in-process vehicles, have access to engineering staff, and confirm specific details on cab configuration, pump panel layout and ground ladder banking. Because of the pandemic, many facilities limit department attendance to three personnel for any plant visit. If your apparatus committee has a large contingent, the option might be to have a virtual pre-construction meeting with the manufacturer’s representative. Should this be the case, the committee should review the technical documentation earlier to confirm that a vehicle’s projected in-service weight will be within the gross vehicle weight rating with an acceptable margin for future changes. Despite the Apparatus Architects emphasizing this over and over, each year, departments find out after contract that the apparatus as presented is overweight and/or requires major changes to the design.
In-person pre-construction meetings normally can take 1–2 days, including some time to tour the manufacturing facility. Virtual meetings can reduce this time. However, all personnel must review the component list, long-verbiage specification and blueprint to become familiar with the component design of the apparatus. These sessions can be taxing, particularly for personnel who haven’t been through the process. If the committee has any particular questions, these should be discussed with the sales representative prior to the meeting to enable staff engineers to address these concerns. At this point, the change order and acceptance process should be reviewed by the committee chairperson, with specific time fences to address when follow-up material or acceptance must be achieved to keep the manufacturing process moving along.Final inspection
Depending upon when your new apparatus was placed on order, the final inspection might be conducted at the manufacturer’s facility. If this is the case, committee members should be assigned specific areas of the vehicle to review, using the long-verbiage specification as the guiding document. At some point during the inspection, if hydraulic lifts aren’t available, personnel should use a creeper to inspect the underside of the chassis to confirm component installation as well as electrical, air and hydraulic lines for proper securement. You also can look for pinched or chaffing lines and heat protection from exhaust system components.
If the apparatus is equipped with a fire pump, as always, time should be reserved in the pump house to conduct an abbreviated pump test and flow test discharges, which will be utilized for preconnected attack lines. A road test, verification of front and rear axle weights and aerial device operational tests all should be completed during the several days of on-site work.
Conducting virtual final inspections can be a challenge, even with an experienced group of committee members. During the past year, the Apparatus Architects conducted a number of virtual inspections, and each was problematic. If your department must rely on a virtual inspection, some suggestions as to how to navigate this process include:
Provide the manufacturer with a detailed list of digital images of areas on the vehicle that the committee desires to show the condition of the apparatus. This should include having the vehicle put on lifts to show all areas of the chassis from the front bumper to the back step; cab interior and exterior; pump panel and inside pump house, showing all piping and wiring runs; and exterior, showing all lighting, paint and graphics. Most manufacturers with which the Apparatus Architects have worked during COVID didn’t charge for providing photos (or videos; see below). The bottom line: Don’t let the apparatus builder provide a walk-around video and call it a day.
One or more videos that confirm road tests, vehicle top speed, and pump and foam operations.
Establish a process that’s acceptable to all parties as to how needed repairs will be completed and the time frame that will be required to accomplish these tasks.
Conduct an in-person follow-up inspection at the local dealership to confirm that all repairs were successfully completed, prior to final acceptance.
Load the apparatus with all tools, equipment, hose and personnel and have the unit taken to a certified scale to confirm the in-service weights, prior to final acceptance and payment.
The latter three points applied prior to COVID, but today, amid COVID, many companies limit the number of personnel who can enter the building, and they might not want to handle the department’s tools. Different geographic areas have different restrictions. Different arrangements might need to be made to ensure that these matters are accomplished. This is to protect all parties. Departments must address these areas up front and early in the process.
Acquiring and placing into service a new apparatus is a detailed process that takes a lot of patience and time to achieve a successful outcome. Doing this during a pandemic will take careful coordination by all parties.
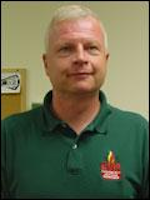
Tom Shand
TOM SHAND, who is a Firehouse contributing editor, is a 36-year veteran of the fire service. He works with Michael Wilbur at Emergency Vehicle Response, consulting on a variety of fire apparatus and fire department master-planning issues. Shand is a member of the Firehouse Hall of Fame.
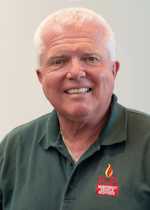
Michael Wilbur
MICHAEL WILBUR, who is a Firehouse contributing editor, retired as a lieutenant in FDNY, where he was last assigned to Ladder Company 27 in the Bronx. He has served on FDNY's Apparatus Purchasing Committee and consults on a variety of apparatus-related issues around the country. Wilbur is a member of the Firehouse Hall of Fame. For further information, access his website at www.emergencyvehicleresponse.com.