The Apparatus Architect: Analyzing Spare and Reserve Apparatus
Fire departments are dealing with extended delivery times and a dramatic increase in costs for new rigs. This is because of a combination of market forces, including supply chain issues and long lead times for major components.
In many instances, fleet managers are having to modify the planned time frames for when new apparatus will be ordered to accommodate these longer production times. Frontline apparatus life cycles are being adjusted as well based on when the new, replacement units will arrive.
Depending on a department’s stated goals for frontline and reserve service, these time frames might need to be reviewed. Often, that results in extended life cycles.
Annex D of NFPA 1901: Standard for Automotive Fire Apparatus (now recognized at NFPA 1900: Standard for Aircraft Rescue and Firefighting Vehicles, Automotive Fire Apparatus, Wildland Fire Apparatus, and Automotive Ambulances) includes life cycle recommendations regarding frontline and reserve apparatus. The standard suggests that apparatus should provide 15 years of frontline service and then be turned over for reserve status. Fire apparatus that are older than 15 years should be evaluated for rebuilding in accordance with NFPA 1912: Standard for Fire Apparatus Refurbishing. NFPA 1901’s Annex D further recommends that apparatus that are more than 25 years old be retired from the vehicle fleet.
Apparatus that are being considered for rebuilding should be evaluated in the following areas:
- Vehicle condition, including maintenance issues, repetitive component failures, corrosion issues and replacement parts availability. Also, does the fully equipped apparatus fall within the parameters of the chassis GVWR?
- Safety enhancements, including seating, seat belts, air bags, vehicle stability, warning lights, nonslip step surfaces and scene lighting
- Does the vehicle meet the needs of the response district in terms of overall size and maneuverability, compartment space, hose load and equipment carried (i.e., ground ladder complement)?
- What is the amortized annual cost of ownership. This figure should include maintenance and repair costs, fuel costs, insurance, and certification testing. Further, how does that annual cost of ownership compare with the original acquisition cost for the apparatus?
- What is the current resale value for the apparatus, and how would the current resale value affect the available funding for the replacement vehicle?
Spare, reserve or recall
The terms spare apparatus, reserve apparatus and recall apparatus might vary from department to department.
Older apparatus that are properly maintained and in good condition generally are relegated to spare or reserve service, for use when frontline units are out of service for preventative maintenance, testing or warranty repairs.
Depending on department resources, engine company units might or might not be outfitted with hose nor with a full complement of tools and equipment. Switching out to a reserve apparatus by an in-service company can take from 45 minutes to several hours, depending on the extent of hose and equipment that’s carried on the reserve rig. The goal should be to minimize the amount of time that an engine or ladder company is out of service and unavailable for responses.
Although the operational terms might differ, some departments maintain fully outfitted apparatus that include tools, equipment, SCBA and radios. These apparatus would serve to be placed into service immediately as needed. These rigs are utilized and staffed during periods of high fire activity, incidents where personnel will operate for extended periods and other emergencies. These units might be called recall or ready reserve apparatus to differentiate them from regular reserve units.
In all cases, these vehicles must be maintained in accordance with department policies as well as the stipulations of NFPA 1911: Standard for the Inspection, Maintenance, Testing, and Retirement of In-Service Emergency Vehicles.How many?
What’s the appropriate number of reserve or spare engine and ladder apparatus for a department? There is no national standard to address this question, so a little research led to the following.
Back when the National Board of Fire Underwriters, which was the predecessor to the Insurance Services Office (ISO), conducted municipal fire protection evaluations of major cities, its requirement was one reserve engine for every five in-service companies and one reserve aerial for every seven in-service truck companies. (The current ISO Fire Suppression Rating Schedule reviews available reserve apparatus and the associated equipment without addressing the total number of reserve apparatus that’s needed.)
Many factors would affect the number of reserve or spare apparatus that are needed to provide adequate fire protection, without having to resort to station brownouts or to companies that respond on nonfunctional apparatus. The fleet manager should maintain data on out-of-service time for each unit that are based on scheduled preventative maintenance, annual certification testing and other repairs. The number of incident responses, the condition of the frontline apparatus and utilization rates can provide data that can be utilized to determine an appropriate ratio of frontline-to-reserve apparatus for a department.
Smaller departments that have modest size vehicle fleets might not possess the resources to operate reserve units of any type. In these instances, regional or shared reserve engine and special service apparatus might be utilized to offset a reduction in services when frontline units are out of service for extended times.
The Apparatus Architects surveyed three fire departments—the Syracuse, NY, Fire Department (SFD), the Arlington County, VA, Fire Department (ACFD), and the Durham, NC, Fire Department (DFD)—to get a glimpse into reserve apparatus fleets.
The SFD staffs nine engine companies and five truck companies along with rescue and squad companies. The department’s spare apparatus fleet consists of three engines and three aerial towers; two fully equipped engines; and one aerial tower. These vehicles serve as recall units. These units are staffed with off duty or overtime personnel during periods of high fire activity and can be placed into service rapidly. Spare heavy rescue and squad apparatus also are maintained in the department’s fleet.
The ACFD operates nine engine companies, three truck companies and two rescue squad apparatus. Four engines, two ladder trucks and one rescue are maintained to backfill when frontline apparatus are out of service for repairs or maintenance. Depending on the type of unit, it can take approximately 45 minutes to switch out an engine and as many as several hours to transfer the equipment on the heavy rescue. The ACFD maintains a well-designed and up-to-date apparatus fleet, which enables reserve apparatus to be similar to the frontline apparatus.
The DFD staffs 16 engine companies, five ladder companies, three quint units, three squad companies and one rescue company. The department maintains five reserve engines, one reserve tower, one reserve ladder and one reserve quint. Similar to the SFD and the ACFD, the DFD’s reserve units are outfitted with hose and ladders, with the equipment having to be transferred over from the frontline apparatus.
About the Author
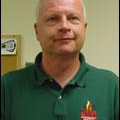
Tom Shand
TOM SHAND, who is a Firehouse contributing editor, is a 36-year veteran of the fire service. He works with Michael Wilbur at Emergency Vehicle Response, consulting on a variety of fire apparatus and fire department master-planning issues. Shand is a member of the Firehouse Hall of Fame.
Michael Wilbur
MICHAEL WILBUR, who is a Firehouse contributing editor, retired as a lieutenant in FDNY, where he was last assigned to Ladder Company 27 in the Bronx. He has served on FDNY's Apparatus Purchasing Committee and consults on a variety of apparatus-related issues around the country. Wilbur is a member of the Firehouse Hall of Fame. For further information, access his website at www.emergencyvehicleresponse.com.