Apparatus Architects: Limit Rust & Corrosion
Since the 1970s, fire apparatus manufacturers have sought ways to minimize rust and corrosion on custom cabs and bodies. Aluminum and stainless-steel body construction have reduced the visible corrosion; however, areas of the vehicle are still subject to damage from road salts and chemicals.
Today, it is rare to look at a 15-year-old apparatus and see extensive body corrosion due the improved construction methods, use of dielectric isolators between dissimilar materials and paint finishes. But when you perform an inspection of the chassis frame rails and components, you may find extensive corrosion on these steel components.
Highway hazards
Over the past few years, both state and local highway departments have begun using magnesium chloride, brine and other chemicals to pre-treat the roadways as well as salt materials during winter storms. Depending upon where you live, these de-icing procedures will make the roadway surfaces safer at the potential expense of coating the underside of your apparatus with these corrosive compounds.
There are several measures that your department can take to mitigate the effects of chemical road treatments, but like any preventative maintenance, they must be handled on a regular basis.
- Conduct at least a monthly inspection of the chassis frame and components to clean any obvious areas of residual road salt and debris, particularly during the winter months.
- Steam-clean the underside of the chassis of all accumulated debris at least twice a year. There are several chemical additives that can be mixed into the water to achieve some degree of protection against salt infiltration into mounting surfaces between cross members and the frame rails as well as in between the frame flanges on double-frame units.
- Ask your maintenance personnel to contact the fleet supervisor from the local highway department to inquire about any particular product or treatment that they utilize to protect their snowplow equipment.
- When developing specifications for new apparatus, consider having the chassis frame rails, cross members and components finish painted to provide a protective layer of paint on all surfaces. Some departments require that the chassis frame and underside of the body be undercoated after assembly. While this provides protection against some corrosion, the undercoating makes visual inspection of these components and subsequent maintenance more difficult.
Some apparatus builders are offering galvanized frame rails and protective coatings to minimize rust and corrosion in these areas. The apparatus committee should inquire about any process that is available along with the warranty provisions that may enhance the longevity of the apparatus. Further, when reading through the standard cab and body structural warranties, you’ll see that they typically cover structural defects or major failure as well as rust through body damage. With the extensive use of aluminum and stainless-steel body materials, it is unlikely that a rust-through condition would occur under normal operating conditions.
In sum
Routine inspection and cleaning of the chassis frame and components will help ensure that these critical areas will provide the life cycle required for the apparatus.
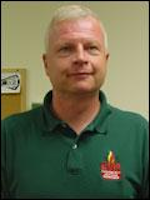
Tom Shand
TOM SHAND, who is a Firehouse contributing editor, is a 36-year veteran of the fire service. He works with Michael Wilbur at Emergency Vehicle Response, consulting on a variety of fire apparatus and fire department master-planning issues. Shand is a member of the Firehouse Hall of Fame.
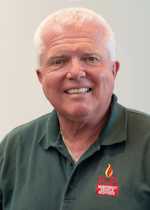
Michael Wilbur
MICHAEL WILBUR, who is a Firehouse contributing editor, retired as a lieutenant in FDNY, where he was last assigned to Ladder Company 27 in the Bronx. He has served on FDNY's Apparatus Purchasing Committee and consults on a variety of apparatus-related issues around the country. Wilbur is a member of the Firehouse Hall of Fame. For further information, access his website at www.emergencyvehicleresponse.com.